テクノロジの絶え間ない進化は最新の自動化ソリューションと結合したオープンな接続性をもたらし、スマートマニュファクチャリングは抽象的な概念から技術的な現実へと劇的に変化しました。
消費者需要は急速に変化し続けていますが、スマートマニュファクチャリングは新たに出現するテクノロジを活用する機会をいかして、これらの進化する要件に対応できます。
スマートマニュファクチャリングは、安全の向上、品質の改善、およびプラントパフォーマンスの最適化による測定可能な結果を提供します。スマートマニュファクチャリングには、人々、プロセス、およびテクノロジなどのさまざまな要素があり、その中で一番重要なのは、どのようにしてそれらすべてを組み合わせてスマートソリューションへの包括的なアプローチを支えるかということです。
データの真の価値
機械やオペレーションから直接取得されるリアルタイムのデータは、スマートマニュファクチャリングの主要な利点です。しかし、データが適切に適用されない場合、またはその後に何の措置も取られない場合、何の利益もありません。
製造エリアに足を踏み入れて、オペレータが問題について頭を悩ませているのを何度も見かけたことがありませんか? オペレータにとって必要なすぐに使用できる情報を与えるためには、使用中の機械は意思決定を改善するためのコンテキストのある実用的な洞察を提供する必要があります。これは、総合設備効率(OEE)に影響を与える課題を把握し、どのような決定が生産性、品質、安全、およびサステナビリティを向上するための適切なレベルへ上げることができるかを推測できるビジネスモデルから始まります。
スマートマニュファクチャリングはプロセスであり、プロジェクトではないことを認識することは重要です。1台の機械、1つのセル、1つのラインから始めて、収集、分析、および提出することのできるデータを検討します。リアルタイムのデータを必要とするときにそれをどのように収集し、どのように使用するかという意図的なデータ戦略が、行動のための基準を提供し、洞察から価値を獲得する方法を提供します。
スマートマニュファクチャリングは行程であり、目的ではありません。テクノロジが進化するにつれて、チャンスも広がります。
スマートであることは、動作データの履歴やリアルタイムの動作データを効率的な方法で活用し、スマートテクノロジを展開してOEEを最適化することを意味します。多分、すでにこの重要な混合した動作データの一部を自体で生成して提供できるデバイスがプラントにあるでしょう。しかし、これらのデバイスからデータを取り出すだけでは、データは得られますがそれは情報ではないことに注意することが重要です。スマートデバイスはそれ自体では製造をスマートにしません。情報を使用するユーザと連携することが、製造をスマートにします。
コンポーネントからPLCまでのスマートシステムの場合、特にOTとITシステムとの間で動作するように設計された情報ゲートウェイソリューションと連携すると、収集したデータは企業全体で共有できます。分析ツールは、トレンドをモニタし、弱点を特定し、トレーニングギャップを浮き彫りにし、オペレーションに負の影響を与える前にダウンタイムを予測する機能を提供します。
スマートソフトウェア
スマートマニュファクチャリングは、状況が理解できる情報を生成するデバイスを接続したシステムとして定義できます。この情報により、人々は正しい判断をすることができ、目的の製造の成果を上げ、目標とした改善を達成することができます。
いかなるスマート・マニュファクチャリング・システムにも以下をサポートするソフトウェアシステムを含む必要があります。
視覚化: これには、MESレイヤ統合、機械データの視覚化、および事業部との連携を含みます。
最適化: 稼働効率、生産性、分析ツールの使用、およびリスク管理に焦点を置きます。
ユーザエクスペリエンス: 任意のユーザの能力、プラントマネージャからオペレータまでのスケーラビリティ、および運用上のインテリジェンスを考慮します。
スマートマニュファクチャリングは、デジタルトランスフォーメーションの入り口です。接続されたスマートデバイスを使用して、プロセスを可視化できる新たな窓を開きます。データと分析ツールを活用し、優れたより速やかな意思決定を実現します。
デジタルの導入
デジタルテクノロジは、人々の生活、働き方、遊び方を大変革しました。テクノロジが引き続き進化するにつれて、テクノロジが提供する恩恵にさらに依存し続けるようになります。これは、特に製造業に関連があります。
コスト削減、顧客満足体験の改善、および収益の増加への圧力がかかります。デジタルを導入する組織は、新しい価値の提案によりビジネスモデルが混乱します。
デジタルエンジニアリングは、いちかばちかの戦略ではありません。従業員が今のところ良く知っていて、気に入っているツールを交換する必要はありません。かわりに、これらのツールをデジタルで拡張し、設計者、生産マネージャ、技術者、および他の人々の作業方法を改善します。まず事業を検討し、デジタルアプローチを使用してどこで物事をよりスマートに、迅速に、またはより良くできるかを判断します。
デジタルエンジニアリングがビジネスを改善できる5つの主要な領域があります。
1. 設計およびプロトタイプ制作
仮想設計と試作は、機械設計をデジタルで構築、試験、評価するのを支援できます。これは、ビジネスで何が可能なのかを変えることができる能力を提供します。これにより、機械を市場に短期間で投入できます。設計上のリスクを削減できます。しかも、より優れた、もっとカスタマイズされた機械を作成できます。
シミュレーションソフトウェアでは、物理法則を3D CADモデルに適用でき、モデルに命を吹き込みます。これにより、モデルを実行し、モデルが人々や他の機械とどのように相互作用するかを確認できます。モデルをVR環境に持ち込み、プラントフロアに自分がいるかのように目の前で機械の動作を監視することもできます。
変更の必要がある場合、部品を買って、数日かけて新しい試作品を作成するかわりに、ほんの何回かクリックするだけでデジタル・ツイン・デザインに変更を加えることができます。機械を市場に迅速に投入するのを支援できるのは、デジタルツインだけではありません。
例えば、オープンデータ交換を使用するソフトウェアの設計では、エンジニアは機械を一度設計するだけで、その後はその設計データをツールでインポートできます。これにより、プロジェクトで設計を書き直したり、再度マッピングする何時間という時間を節約できます。再利用可能なコードにより、最初から再設計する必要がなく、成功した既存の機械を基にして構築できます。
2. 立上げ
機械を現場に持ち込んでから制御試験を実施することは、大失敗を招く原因となります。恐らく、操業開始日が近づいてお客様の側に立つまで、機械とその制御システムが調整されているかどうか分かっていないでしょう。機械が予想以下の性能、または仕様に達しないことを発見するかも知れません。最後の瞬間にこれらの問題を解決することは、高額な費用がかかり、納期を逸することにもつながります。
仮想コミッショニングは、こうした問題に終止符を打つことができます。機械設計および制御システムの実際のオペレーションのロジックの両方が動的なデジタルツインを作成することにより、お客様のプラントのフロアに機械を据え付けるずっと前、初期の設計段階で問題を発見できます。仮想コミッショニングでは、リソースを投入する前に、機械やコントローラを実際に動作させ、徹底的に検証できます。
ダイフクウェブ社はシミュレーションソフトウェアを使用して、現場に出荷する前に社内でマテリアル・ハンドリング・システムのPLCコードを試験しています。ある空港プロジェクトでは、これは大きな費用の削減をもたらしました。ダイフクウェブ社の上級制御エンジニアであるグレッグ・スウィッシャー氏は次のように述べました。「通常、当社の社員は現場で何か月も費やしています。ところが、当社のエンジニアが現場に到着してお客様が検収するまで、わずか3週間まで時間を縮めることができました。」
「通常、当社の従業員は現場で何か月も費やします。ところが、当社のエンジニアは現場に到着してからお客様が検収するまでわずか3週間に時間を縮めました。」– グレッグ・スウィッシャー氏、ダイフクウェブ社の上級制御エンジニア
3. トレーニング
仮想トレーニングは、 機械とオペレータが共に現場にいる必要をなくします。デジタルツインにより、機械が到着する前に従業員をトレーニングできます。VRヘッドセットを装着するか、画面で作業するかのどちらかで、従業員は安全かつ実体験のような仮想環境で技術とコンピテンシを身に着けることができます。仮想トレーニングの最大の利点の1つは、自由さです。
いつでも、どこでもトレーニングを実行できます。必要としている誰にでも、必要なときにいつでも、必要な場所どこにでも柔軟にトレーニングを提供できます。さらに、仮想トレーニングには現実世界のトレーニングと同じ制限がありません。従業員は最適なオペレーションで生産工程を維持する方法を学ぶことができ、シミュレーションされた故障や物理的な複製では実施不可能な過酷な条件での試験を行なうことができます。これにより、生産段階で同様の事故に対応する準備が整い、究極的にダウンタイムを短縮できます。
従業員は自由に仮想トレーニングでミスをすることができます。生産を混乱させることを心配する必要はありません。オペレータが何か間違った操作をした場合、その処置は改善のために記録しておくことができます。 さらに、従業員は実際の生産に従事する前に、トレーニングで必要な自分の業務遂行能力を証明することもできます。
経験を積んでいる従業員が退職し、新たな世代がとってかわると、仮想トレーニングは従業員がもっとなじみのある方法で仕事を学ぶのに役立ちます。自宅にあるタブレットやVRヘッドセットのようなデバイスを使用でき、トレーニングは仮想環境で学習をゲーム化して効果を上げることができます。
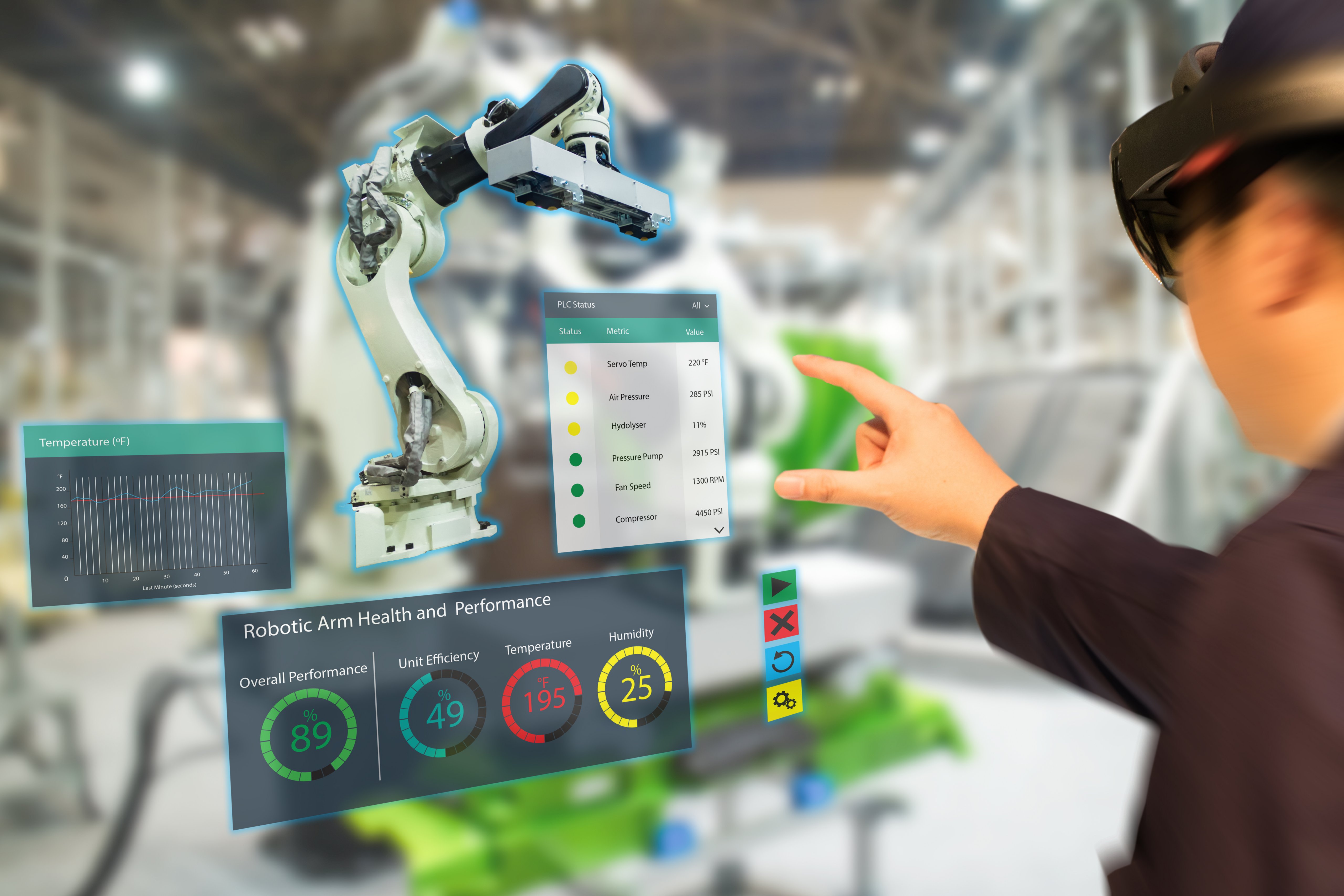
4. オペレーション
デジタルエンジニアリングの価値は、機械の立上げが完了し、オペレータのトレーニングが完了するとなくなるわけではありません。生産が始まると、デジタルツインはプロセス、機械、制御を模倣し、プラントの作業者がオペレーションについて学習し、変更を試すのを支援できます。ますます増加する情報のデジタルスレッドが、生産をどのように改善できるかについての洞察を明らかにできます。
あらゆるタイプのオペレーションは生産の改善を継続して進めると新たなレベルに達することができ、デジタルスレッドからの洞察を使用してその場で調整できます。トライアルラインのスタートアップと生産スケジューリング、および製品構成と量を最適化するためにシーケンシングを使用します。品質、信頼性、およびスループットを改善するために機械構成を試してみます。
さらに、デジタルスレッドを使用してプロセスの異常を検出し、品質に影響がでる前に操業上の問題を明らかにし、ダウンタイムを無用にします。新製品や機械を試験運転してスループットを最適化し、下流の工程のボトルネックのような問題を避け、貴重な生産時間を確保することができます。
あるグローバルな製造メーカは、MES (製造実行システム)と一緒にデジタルスレッドを実装し、お客様へのリードタイムの50%の短縮、欠陥部品の50%の削減、生産性の4%の向上を実現しました。
5. メンテナンス
メンテナンスチームは、デジタルシミュレーションとリアルタイムまたは予知による洞察さえも使用して、今までにない方法でダウンタイムに取り組むことができます。デジタルスレッドを流れるデータのおかげで、技術者は発生時点で問題を検出し、ダウンタイムを防止し、最小化できます。
このデータには、メンテナンスが必要な時期を技術者に通知できる制御システムデバイスからの健全性データおよび診断データなどが含まれます。データは、今日、稼働時間の維持に不可欠なスイッチレベルのアラームからのネットワークデータなども含みます。
ダウンタイムの発生予測により、メンテナンスチームがダウンタイムにまったく対応する必要がないのが理想的な姿です。これは予測分析の実用化のおかげで、今後ますます可能になっていきます。これらの分析ツールは機械学習や人工知能を使用して、オペレーションを学習し、早期に機械の問題を特定し、それらの問題を技術者に警告します。技術者は、計画されたダウンタイムの間にメンテナンスをスケジュールできます。
デジタルツインは、いろいろな方法でMTTRの改善を支援できます。まず、仮想トレーニングを行なうことにより、技術者はダウンタイム問題が発生したときに初めてトラブルシューティングするのではなく、事前に問題に対して準備できます。問題が実際に発生すると、技術者はARテクノロジを使用して実際の機械に診断または作業指示を重ね合わせて、迅速に診断し、問題を解決できます。
「産業組織が労働力の移行を管理するので、予測分析ソリューションはメンテナンス決定を保証でき、プロセスがキャプチャされ、新入社の従業員はそれを繰り返すことができます。」– ARCアドバイザリグループ、デジタルツインのロードマップ: 事後保全から処方的保全へ
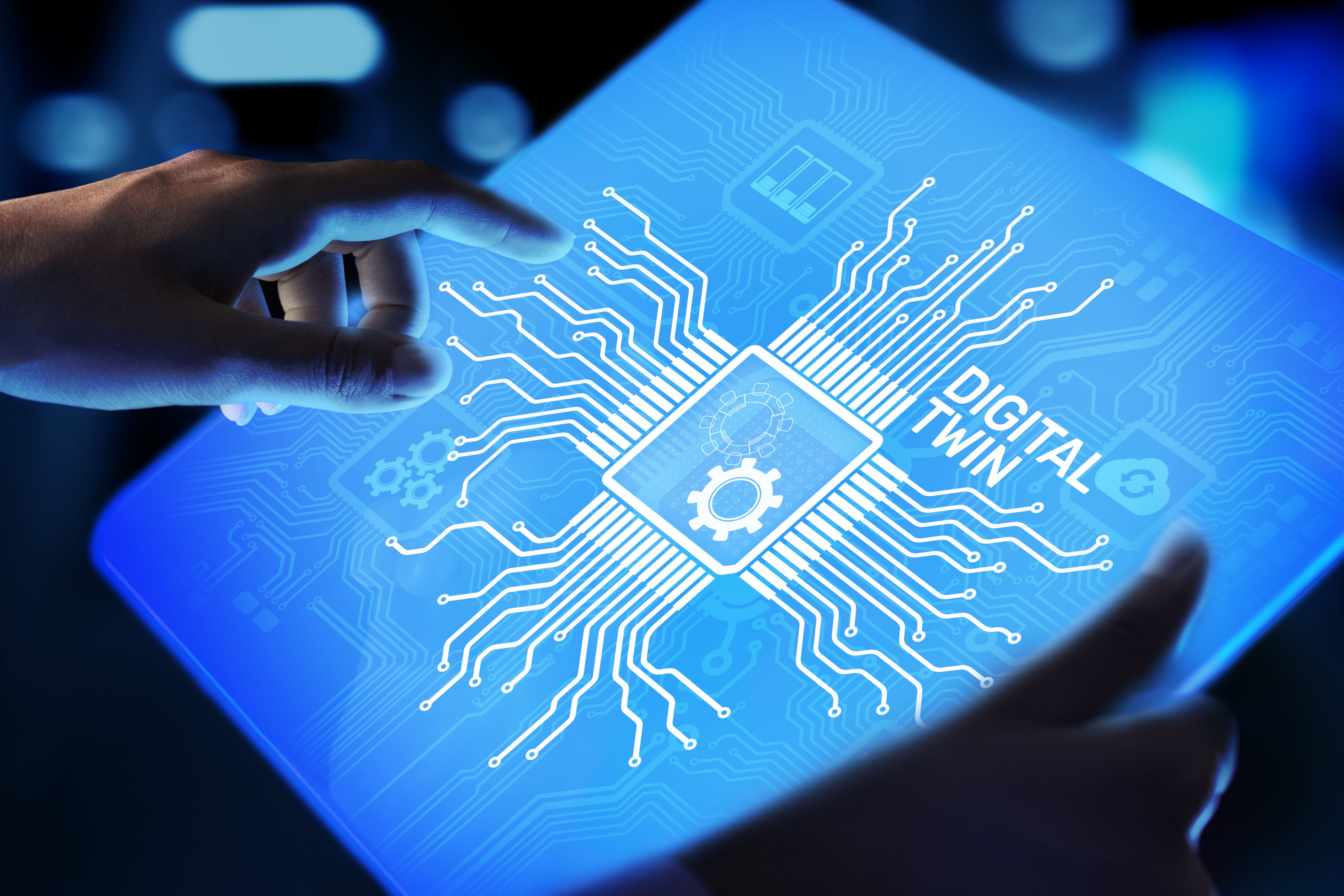
よりスマートなサプライソリューション
デジタルの行程のどこにいようと、スマートコンポーネントおよびスマートオブジェクトをコントローラレベルで搭載している、よりスマートな、より安全な、もっと接続された、セキュアな機械をサプライヤに要求するのは時間と労力をかける価値があります。これは、接続されるとすべてのデータが整理され、すぐに使用可能な状態でそこにあり、接続した瞬間にその価値を獲得できます。
エンドユーザとして、機械装置メーカ(OEM)と取り組み、指定し、質問する必要があります。ご自分にこう尋ねてみてください。「この機械がスマートテクノロジを搭載したらどんな付加価値を得ることができるだろうか?」 それから、まったく同じ質問を機械装置メーカに尋ねます。
価格が購入を決定するときの第一の基準であるべきではありません。オペレーション、消費、生成するデータが提供できる追加の価値など、資産の全生涯コストを考慮することが重要です。サプライヤと緊密に協力し、スマートに対する熱望を説明し、それからスマートマニュファクチャリングの目標を達成することのできるテクノロジの利用に挑戦します。
オペレーションが、以下のような恩恵を得ることができるか想像してみてください。
- ユーザがもっと積極的に行動でき、オペレーションの洞察を得ることができる動作データ
- 短期間での投資の回収および稼働時間の拡大
- システム統合、オペレーション、およびメンテナンスを簡略化する設計のフレームワークおよびオペレーションツール
- 共通のプラットフォームでの統合
- 機械アクセスの改善、ダウンタイムの短縮、および再起動時間の削減によって安全と生産性を強化する安全機能
- 従業員を危険にさらすのを最小限にする速度診断およびトラブルシューティングへのセキュアなリモートアクセス
スマートマニュファクチャリングでは、今ではこれが現実となります。プラントレベルと企業ネットワークを統合し、人々、プロセス、およびテクノロジをセキュアに接続することにより、何が可能なのかを再定義できます。
可能性の再定義
今では、これまで以上に、ビジネスは少ない労力で多くの生産を上げようと全力を尽くしています。これに加えて、変化する人口構成が、オペレーションで従業員を配置する企業の能力を圧倒し、退職、経済拡張、技術発展によって製造メーカや事業者に労働力の課題を生み出しています。
現在の大半のビジネス成果は、ほぼ知識駆動型オペレーションとスマートで柔軟な製造に基づいています。自社の労働力の強みと能力を最適化する、すぐに活用できる洞察をオペレータ、メンテナンス技術者、エンジニア、マネージャ、および経営者に提供することは、スマートマニュファクチャリングの最重要な要素です。
優れたデータアクセスにより明らかになった新しい洞察は、ボトルネックの削減、需要ベースの意思決定の実装、メンテナンスの改善を支援できます。デジタル化を進めるほど、ダウンタイムを短縮し、収益性を改善できます。
バリューチェーン全体にわたるリアルタイムなコラボレーション、新しいラインとプロセスのバーチャル検証、データサイエンスの簡略化、製造の柔軟性の向上から恩恵が得られます。
オペレーションをデジタル化して変革することは、可能性を解き放ち、企業パフォーマンスのほとんどあらゆる側面を改善します。
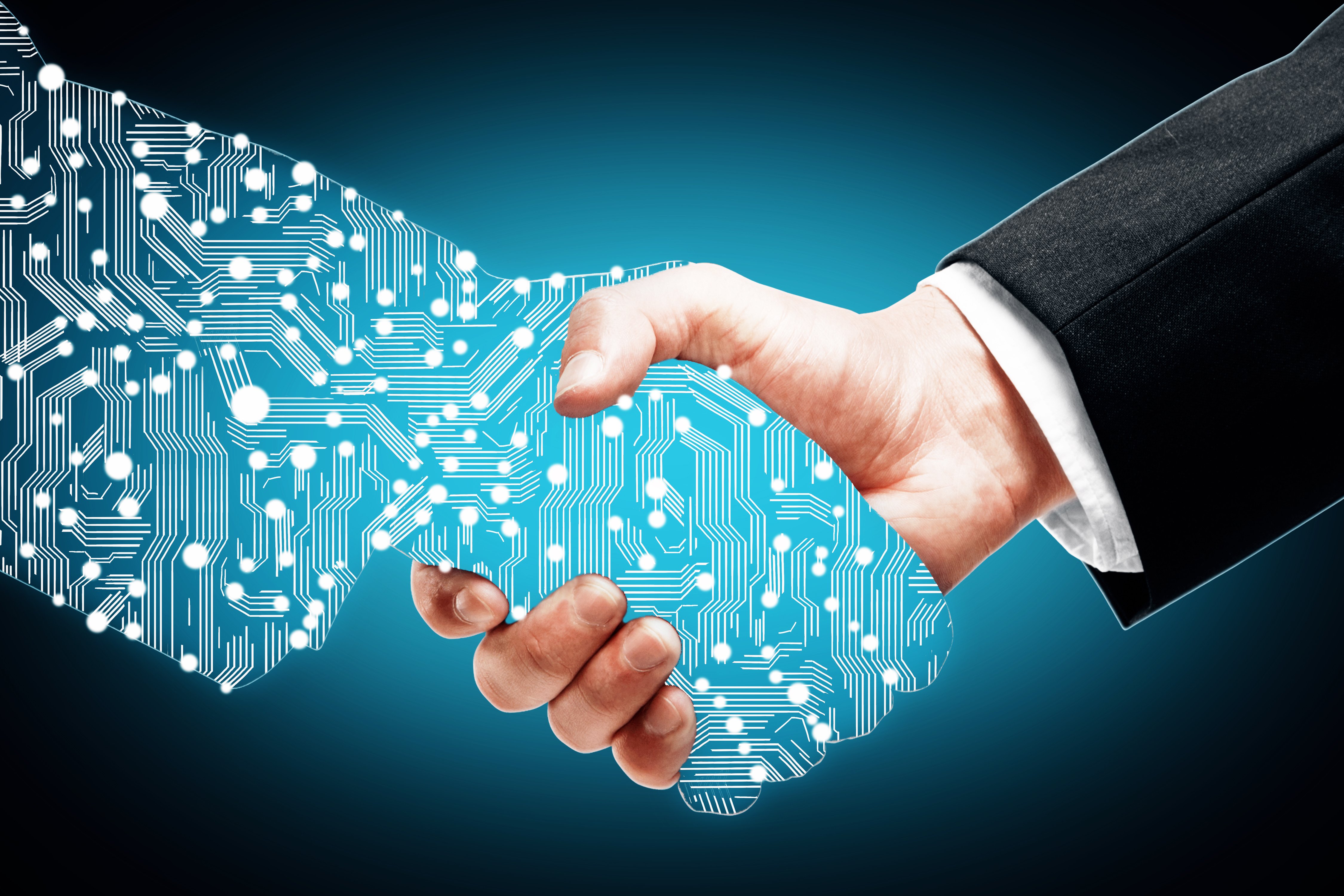