細胞生物学の進歩は、過去10年で医薬品業界に劇的な変化をもたらしました。高分子療法や生物学的療法の拡大は言うまでもありません。超大型新薬がまだまだ大きな存在を占めている一方で、新しい技術が、より個人に合わせたオーダーメイドの治療を現実のものにしています。
もちろん、科学的発見には値札とメーカの課題が付き物です。バイオテクノロジ企業の場合、問題は発見の速いペースに遅れずについていき、厳しく規制された環境で迅速かつコスト効率よく新製品を患者に届けることです。
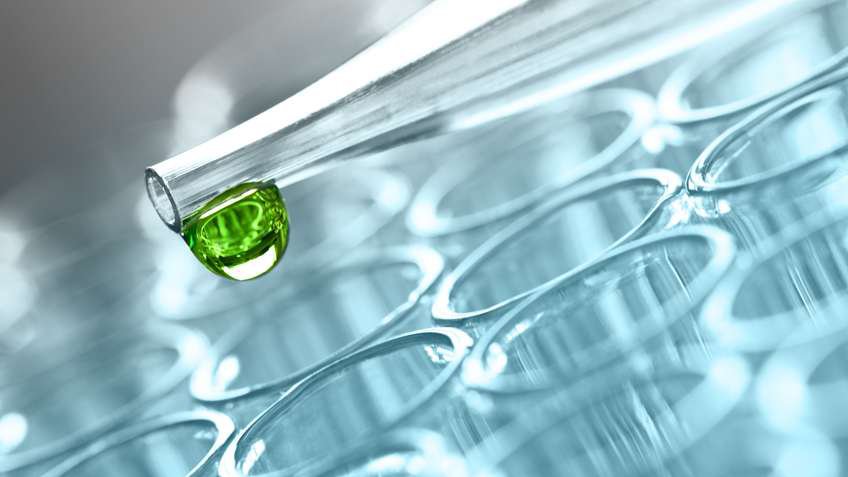
この課題に対応するために、多くのバイオテクノロジ企業が、カスタマイズされた少量の製品を短時間で生産するための単一用途機器、事前に検証済みのスキッド、その他の柔軟な製造アプローチに取り組んでいます。
これらの新しい「最先端施設」では、従来のハード配管のステンレススチールでできた施設の場合は通常3年または4年かかっていたスタートアップ時間が、6ヶ月から12ヶ月に大幅に短縮されます。
研究から生産までの並外れた拡張性を特長としたこの施設は、代替製品の生産用に短時間で再構成できるため、設備投資および関連リスクを最小限に抑えることもきます。
しかしながら、今後何年にも渡って利益を生み出す施設を作るには、大がかりなプランニングが必要です。パフォーマンスと柔軟性を最大限に向上させるには、バイオテクノロジ企業は工場の稼働、ならびにオートメーションおよび統合戦略の両方を、コンセプト段階から厳密に検討しなければなりません。
最初に考慮するべき2つの重要な問題があります。
オートメーションシステムをどのように使用して、オペレータのパフォーマンスを向上させ、インフラ要件を最小限に抑え、定期的なレポートを簡単に行なえるようにするのか?
ステンレススチールでできた、高度に自動化された医薬品工場に慣れているエンジニアはみな、単一用途施設でのモバイル機器のプラグ&プレイ性と、人が行なわなければならない作業量に衝撃を受けるでしょう。
実際に、上流リアクタでのシングルバッチの生産に必要とされる手動操作は、使い捨てビニール袋の挿入から正しい機器、栄養素、チューブなどが所定の場所にあることの確認にいたるまでの、800~900にも上ります。しかも、セットアップのどの時点でエラーが発生しても、バッチが失敗する原因となります。
オートメーションシステムをさまざまな方法で使用することによって、エラーの可能性を最小限に抑え、検証メソッドを改善するのを支援できます。例えば、自動機器認識および検証システムを制御プラットフォームに組み込んで、機器の配置を追跡し確認することができます。
また、制御システムに視覚的な支援を組み込めば、プロセスステップ内でオペレータは指示を参照でき、紙ベースの取扱説明書に対して大幅に作業効率を改善できます。
どのように機能するのか?
オペレータが、転送パネルでポイント1とポイント4を接続する必要があるとします。これらのポイントは、該当するチューブの接続に沿って電子インターフェイス上に点灯します。
ビジュアルガイダンスのほかに、システムは検証まで行なうことができます。例えば、原料や機器を追跡するために、シリアル番号の入力やバーコードのスキャンをオペレータに指示でき、入力やスキャンデータはバッチレコードに自動的に記録されます。
その上、オートメーションおよび情報技術の発達のおかげで、製造メーカは多額のインフラ投資や複数のインターフェイス端末なしで、一貫した視覚化を実現できます。
最新のシンクライアント技術を使用して、作業員はタブレットで必要な操作を実行できます。さらに、位置検出機能がモビリティをサポートし、また、オペレータが特定の作業を行なうための正しい場所にいることを確認することで、セキュリティを維持するのを支援します。QRコード、Bluetoothビーコン、Wi-Fi、GPSなどの位置レゾルバが、モバイルユーザおよびデバイスが認可されたエリアでのみ内容を受信していることを確認します。
施設全体で統合と一貫性を実現するための最良の方法は?
根本的には、単一用途施設は複数の機器ベンダーが提供する複数のプロセススキッドで構成されています。通常、制御プラットフォームとソフトウェアセットはサプライヤごとに異なっています。さらに、特定の機械装置メーカ(OEM)内部でも、機器のタイプが異なると、使用される制御システムも異なることがあります。
その結果として生じた「オートメーションの島々」が、工場全体での一貫したオペレーション、保守、エンジニアリングの大きな障害となっています。オペレータはすべてのシステムを学習しなければならず、また、多くの場合、複数のスペアおよびサービス契約を維持する必要があります。
その上、一貫したデータフローがないため、データの整合性とコンプライアンスに問題が生じる可能性があります。
道は未来に続いているか? バイオテクノロジ企業とそれに協力する機械装置メーカ(OEM)は次第に、一貫した構造、および一貫したソフトウェアセットを実現する最新の分散制御システムに基づいた統合へのアプローチを探るようになっています。この拡張性に富んだ情報対応アプローチは、比類のない接続性と柔軟性を約束します。
多くの点で、バイオテクノロジ企業の将来の展望は今までにないほど明るくなっています。単一用途施設と生物製剤の製造に習熟したオートメーションコンサルタントが、お客様の新しい施設を真に未来を見据えたものにするための戦略を決定するお手伝いをします。
公開 2017/12/13