お客様へのご提案
ダウンタイムに最適な時期はいつでしょうか?
ほとんどの場合、答えは「適した時期がないのはよいことです」です。本当の問題は、アップグレードが避けられない状態になるまでに、老朽化したDCSがどれだけの間だましだまし動かすことができるかということです。
今日のパルプおよび製紙工場は、一定の圧力の下で稼働しており、生産コストを削減し、歩留まりを向上させています。「(まだ)壊れていない場合は、修正しないでください」とは、リスクの高いアプローチであり、従来のシステム、特に生産性が向上したDCSの場合です。
これは、古くなったパルプバッチダイジェスタを利用しているお客様が見つけたものです。これはパルプ工場で最も複雑なプロセスで、ここで問題が起こるとあらゆる場所に問題を引き起こします。
その時が来ましたか?
ほとんどの古いシステムと同様に、このお客様(クイック・サービス・レストラン用の特別な食品ラッパーの生産者)は、スペアの欠如、時代遅れの機器サポートリソース、およびプロセスの可視性に関する重大な問題に直面しました。オペレータは、さまざまなステーションやビューからバッチ調理プロセスを管理することを余儀なくされました。
従来のDCSの非効率性は、移行のダウンタイムリスクを上回りました。
1枚のガラス
新しいバッチダイジェスタ制御は、以下のように設計されています。
- 未調理の廃棄の減少と均一なカッパを含む、ダイジェスタの回転率を改善
- 調理中のダイジェスタの温度制御を改善
- 充填中のチップの事前蒸し中の蒸気使用量を削減
- テレビン油の収量を増やす
これらの目標を達成することに加えて、DCSをアップグレードすると、従業員に大きなメリットがもたらされました。オペレータは、「1枚のガラス」を使用して1つのシステムで必要なすべての情報を入手できるようになりました。
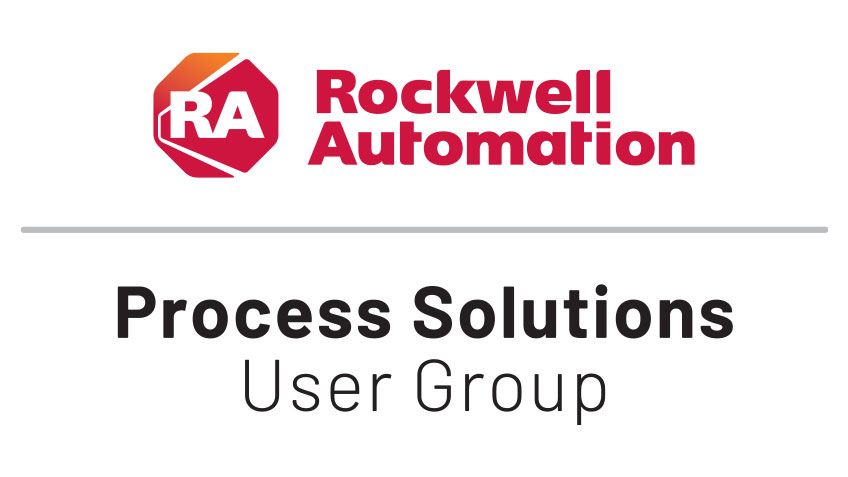
DCSスキルのギャップを減らすことで一貫性が向上
他のプロセスのPlantPAx®DCSにすでに慣れているオペレータは、このニッチアプリケーションの知識を簡単に変換できます。トレーニング時間を節約し、スキルギャップの影響を減らしたり、新しいシステムを学習および管理するための知識不足を減らすことができます。
バッチダイジェスタ制御は、外気温や湿度などのいくつかの要素に基づいてパルプの調理を調整できるようになり、より一貫した結果を得るために自動的に改善を行なうことにより、各調理を最適化します。このダイジェスタの最適化は、シフトごとに(オペレータに関係なく)標準化された運用と相まって、予想される結果(ダウンタイムの短縮)だけでなく、製品の数量と品質の向上にもつながりました。
結論: ボトルネックが少なく、1日当たりのバッチ数が増えます。
これはニッチなアプリケーションですが、達成された利点は他のプロセス産業にも適用できます。オペレータはシステムをより簡単に扱うことができ、プロセスに対する可視性が高くなります。経営幹部は、生産の増加と歩留まりの向上など、約束された利益を実現しています。
このお客様は、2019年11月18~19日にシカゴで開催されたプロセス・ソリューション・ユーザ・グループ(PSUG)において、このプロジェクトの詳細を提示し、PlantPAx最新のDCSがどのように運用を改善したかを説明いたしました。
公開 2019/10/30