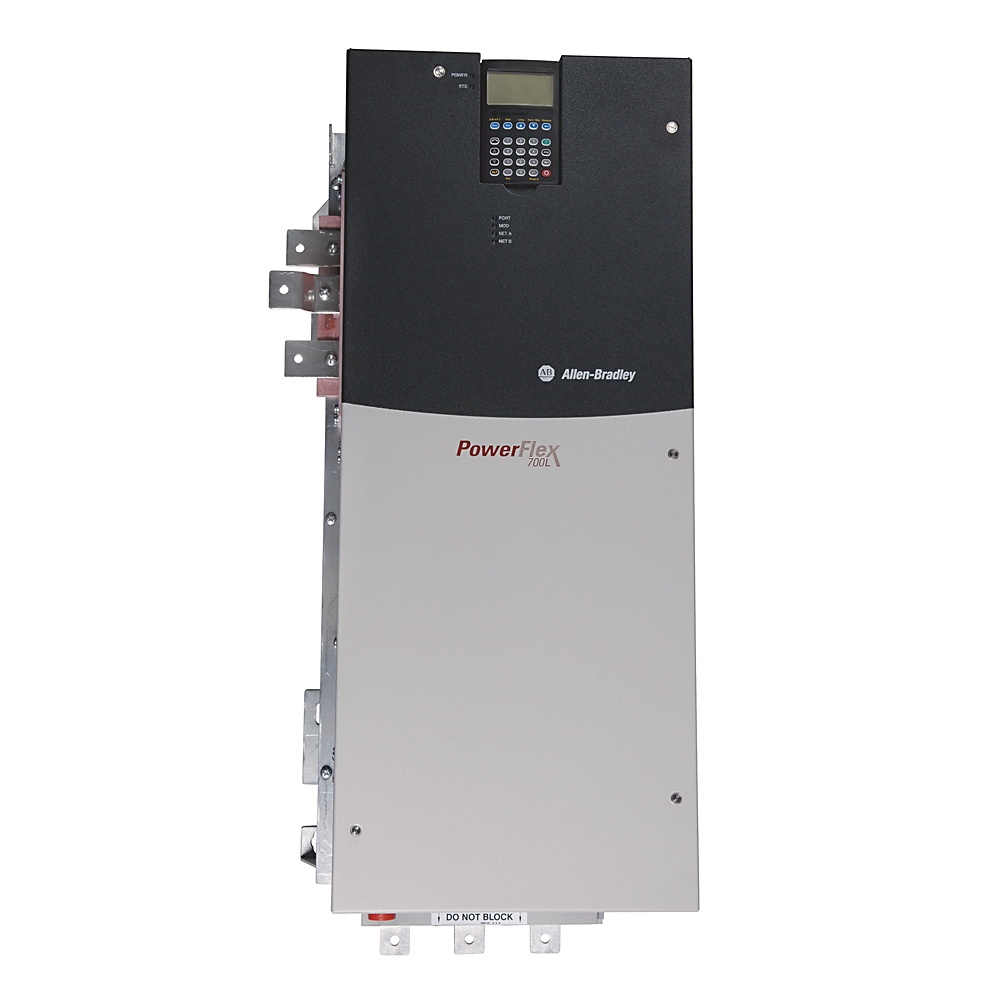
PowerFlex 700L AC Drive 20L
Rockwell Automation announces that as of
June 30, 2022,
the PowerFlex 700L AC Drive 20L will be discontinued and no longer available for sale.
Customers are encouraged to remove references to the affected product(s).
Discontinued Date:
June 30, 2022
Replacement Category:
Engineering Replacement
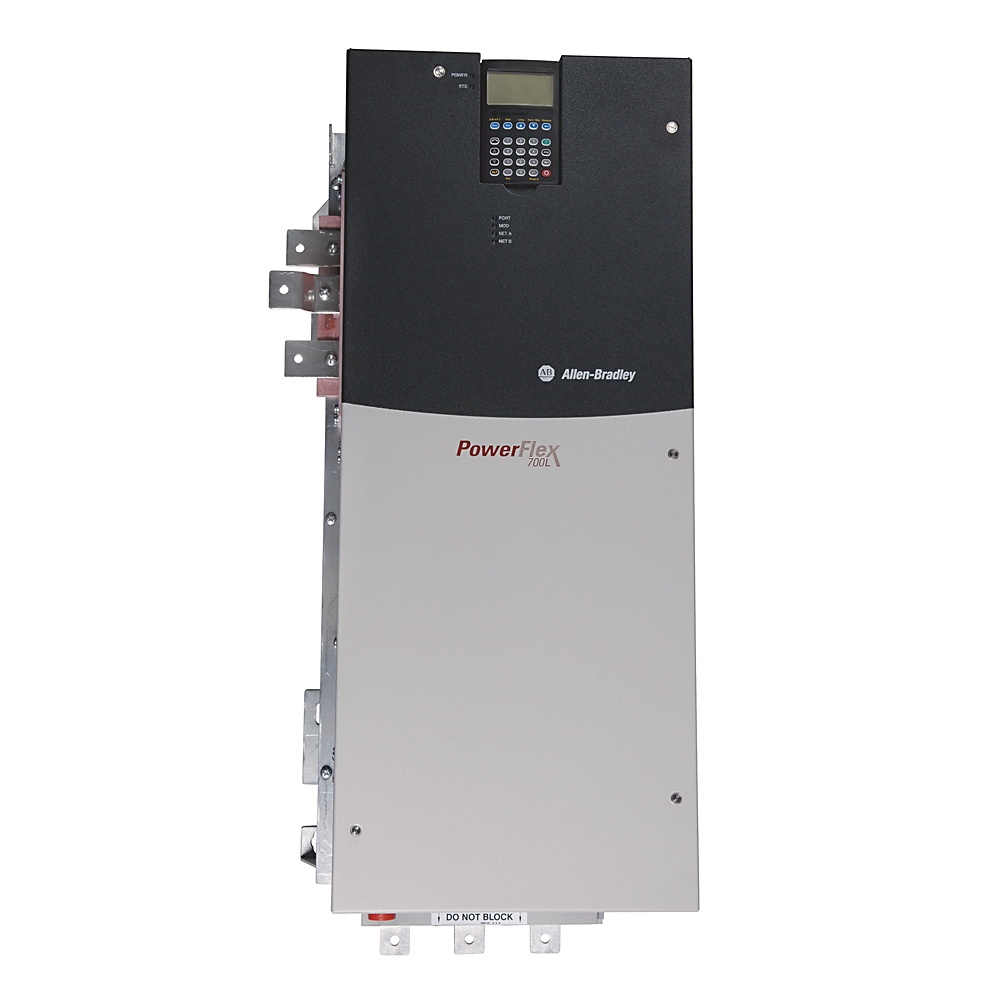
Rockwell Automation announces that as of
June 30, 2022,
the PowerFlex 700L AC Drive 20L will be discontinued and no longer available for sale.
Customers are encouraged to remove references to the affected product(s).
Discontinued Date:
June 30, 2022
Replacement Category:
Engineering Replacement
Coolant | Water |
---|---|
Equipment Type | Complete Regenerative Drive |
Feedback Options | Standard Encoder |
Product Family | PowerFlex 700L AC Drive |
Width | 423.8 mm |
---|---|
Height | 955.7 mm |
Depth | 566.1 mm |
Weight | 186 kg |
Terminal bolt size | M8, PE, motor ground bus bar for power terminal |
Custom option | None |
Recommended tightening torque | 40 Nm (354 in-lb)(±10%), PE, motor ground bus bar for power terminal |
SHLD terminal | Terminating point for control wiring shields on the drive for control terminal |
DC bus test point socket | 4 mm socket for DC bus voltage measurement only (2 terminals: DC+, DC-) |
Motor lead lengths | 76 m (250 ft) total |
Wire strip length for active converter cassette terminal blocks-P1 & P2 | 8 mm (0.31 in) for control terminal |
Wire strip length for terminal block-TB1 | 8 mm (0.31 in) for control terminal |
Wire strip length for SHLD terminal | 10 mm (0.39 in) for control terminal |
Wire strip length for PS- and PS+ terminal | 10 mm (0.39 in) for control terminal |
Terminal block-TB1 1b 7: +24V (digin) | Drive-supplied +24V DC for control terminal |
Recommended tightening torque for active converter cassette terminal blocks-P1 & P2 | 0.8 Nm (7 in-lb)(±10%) for control terminal |
Recommended tightening torque for terminal block-TB1 | 0.9 Nm (8 in-lb)(±10%) for control terminal |
Recommended tightening torque for SHLD terminal | 1.4 Nm (12 in-lb)(±10%) for control terminal |
Recommended tightening torque for PS- and PS+ terminal | 0.6 Nm (5.3 in-lb)(±10%) for control terminal |
PS- terminal and PS+ terminal | 300V DC auxiliary control voltage for control terminal |
Wire size for terminal block-TB1 | 0.2 mm² to 4 mm² (#24 AWG to #10 AWG) for control terminal |
Wire size for PS- and PS+ terminal | 0.5 mm² to 4 mm² (#22 AWG to #12 AWG) for control terminal |
Wire size for active converter cassette terminal blocks-P1 & P2 | 0.3 mm² to 3.3 mm² (#22 AWG to #12 AWG) for control terminal |
Wire size for SHLD terminal | 0.3 mm² to 2.1 mm² (#22 AWG to #14 AWG) for control terminal |
Active converter cassette terminal blocks-P1 & P2 | Active converter AC power and control wiring for control terminal |
PE, motor ground bus bar | Terminating point for wiring shields and grounds for power terminal |
Terminal block-TB1 1b 8: gate enable | Enables the firing of the IGBTs. Factory-installed jumper from terminal 1b 7 to terminal 1b 8 allows firing of the IGBTs for control terminal |
Terminal block-TB1 1b 5: +12/+24V cooling loop 1b 6: cooling loop return | Drive control wiring: output dry contact (12V DC/24V DC @ 2A max.) indicating the drive is powered and has completed precharge for control terminal |
Degree of protection (IP) | IP00 |
---|---|
Shock | 10 G peak for 11 ms duration (±1.0 ms), three shocks in each direction, in each axis |
PWM frequency | 4 kHz |
Vibration | 2 mm (0.07 in.) displacement, 1 G peak Alitude, 1 mm (0.04 in.) displacement from 2…13.2 Hz, 0.7 G acceleration at 13.2 Hz to 1.0 G acceleration at 55 Hz, 1 G acceleration from 55 …512 Hz Duration: ten logarithmic sine sweep cycles per axis, at sweep ra |
Number of analogue outputs | 2 None |
---|---|
Mains voltage | 400 V |
DC bus undervoltage shutoff/fault | 300V @ 400V |
DC bus overvoltage trip | 815V @ 400V |
DC nominal bus voltage | 600V @ 400V |
Brake IGBT | No brake IGBT |
Input voltage | 400V AC, 3-phase, 60 Hz |
Torque regulation without feedback | ±5%, 600 rad/sec bandwidth |
Torque regulation with feedback | ±2%, 2500 rad/sec bandwidth |
Internal communication module | EtherNet/IP |
AC input undervoltage trip | 340V @ 400V |
Displacement power factor | 0.98 across entire speed range. |
Circuit breaker current rating, max | 900A @ 400V AC, 3-phase, normal duty |
Motor circuit protector current rating, max | 600A @ 400V AC, 3-phase, normal duty |
Non-time delay fuse current rating, min | 500A @ 400V AC, 3-phase, normal duty |
Non-time delay fuse current rating, max | 900A @ 400V AC, 3-phase, normal duty |
Logic control ride-thru | 0.5 s minimum, 2 s typical |
Brake resistor | No internal brake resistor |
Input current rating | 360A @ 400V AC, 3-phase, normal duty |
Documentation | No documentation |
Carrier frequency | 2, 4 or 8 kHz drive rating based on kHz |
Encoder quadrature | 90°, ±27° at 25 °C |
AC input overvoltage trip | 528V @ 400V |
Electronic motor overload protection | Class 10 motor overload protection according to NEC article 430 and motor over-temperature protection according to NEC article 430.126 (A)(2). UL 508C file E59272 |
Dual element time delay fuse current rating | 500-750A @ 400V AC, 3-phase, normal duty |
Heat sink thermistor | Monitored by microprocessor overtemp trip |
Equipment type | Complete regenerative drive |
Stop modes | Multiple progmable stop modes including RA, Coast, DC-brake, RA-to-hold and S-curve. |
Human interface module | No HIM (blank plate inserted) |
Acceleration/deceleration | Two independently progmable accel and decel times. Each time can be progmed from 0...3600 s in 0.1 s increments |
Frequency accuracy | Digital input: within ±0.01% of set output frequency |
Number of digital inputs | 6 None |
Number of digital outputs | 3 None |
Number of analogue inputs | 2 None |
Supporting protocol for DeviceNet | True |
Additional configuration | None |
Application in industrial area permitted | True |
Supporting protocol for EtherNet/IP | True |
Mains frequency | 60 Hz |
Actual short circuit rating | Determined by AIC rating of installed circuit breaker. |
Output current (with 400V AC induction motor) | Normal duty: 540 A @ 150% of continuous current for 3 s |
Watt loss | Complete drive: 7900 W @ 400V total liquid |
Feedback option | Standard encoder ftdback for enhanced control, vector control |
Enclosure type | IP00/NEMA/UL Type open |
Output current rating | 360A @ 268Hp (200 kW) normal duty, 200 Hp (150 kW) heavy duty, frame 2 |
Control options | 700 vector control with 24V DC I/O |
Drive overcurrent trip | Software overcurrent trip: 200% of rated current (typical) |
Efficiency | 96.2% at rated A, nominal line volts |
Encoder supply | 12V @ 250mA. 12V @ 10mA minimum inputs isolated with differential transmitter, 250 kHz maximum |
Output frequency | 0 to 420 Hz |
Speed control | Speed regulation with ftdback: 0.001% of base speed across 120:1 speed range 1000:1 operating range 250 rad/sec bandwidth |
Current limit capability | Proactive current limit progmable from 20...160% of rated output current, Independently progmable proportional and integral gain |
Selectable motor control | Sensorless vector with full tuning. Standard V/Hz with full custom capability and vector control with force technology (with and without ftdback). |
Frequency control | Speed regulation with slip compensation (volts per Hz mode): 0.5% of base speed across 40:1 speed range 40:1 operating range 10 rad/sec bandwidth |
Input phases | 3-phase input provides full rating for all drives. |
Control method | Sine coded PWM with progmable carrier frequency |
Encoder requirements | Encoders must be line driver type, quadrature (dual channel) or pulse (single channel), 8...15V DC output (3.5...6V DC @ 5V encoder), single-ended or differential and capable of supplying a minimum of 10 mA per channel. Maximum input frequency is 250 kH |
Number of phases output | 3 None |
Number of phases input | 3 None |
With control element | True |
Supporting protocol for TCP/IP | True |
Supporting protocol for PROFIBUS | True |
Supporting protocol for CAN | True |
Supporting protocol for Modbus | True |
Application in domestic- and commercial area permitted | True |
Encoder duty cycle | 50% ±10% |
Input frequency tolerance | 47...63 Hz |
Input frequency, ,max | 400 kHz ftdback |
Output voltage range | 0 to rated motor voltage |
Encoder type | Incremental, dual channel |
Short circuit trip | Phase-to-phase on drive output |
Ground fault trip | Phase-to-ground on drive output |
Control logic noise immunity | Showering arc transients upto 1500V peak |
Line transients | Up to 6000 volts peak per IEEE C62.41-1991 |
Output power bus bar | Motor connections (U/T1, V/T2, W/T3) for power terminal |
Input power bus bar | Input power connection (R/L1, S/L2, T/L3) for power terminal |
Intermittent overload | 110% overload capability for up to 1 min, 150% overload capability for up to 3 s |
Short circuit current rating | To match specified circuit breaker capability, less than or equal to 200000 A symmetrical. |
Encoder input voltage supply | Dual channel plus marker, isolated with differential transmitter output (line drive) incremental, dual channel quadrature type 5V DC or 12V DC (5V DC requires an external power supply), 320 mA/channel for ftdback |
Pressure drop from drive inlet to drive outlet at minimum coolant flow rate | 1.58 bar |
---|---|
Estimated amount of coolant | 15.1 L |
Coolant temperature | 0 °C |
Altitude | 1000 m (3280 ft) at rated current |
Surrounding air temperature without derating, max | 0 to 50 °C (32 to 122 °F) @ IP20, NEMA/UL Type 1 |
Coolant type | WEG50 equals good quality or distilled water with approved inhibited ethylene glycol, 50% glycol by volume or WPG50 equals good quality or distilled water with approved inhibited propylene glycol, 50% glycol by volume. |
Atmosphere | Drive must not be installed in an area where the ambient atmosphere contains volatile or corrosive gas, vapors, or dust, If the drive is not going to be installed for a period of time, it must be stored in an area where it will not be exposed to a corrosi |
Coolant flow rating | 30.3 l/min |
Relative humidity | 5...95% noncondensing |
Storage temperature | -40...85 °C (-40...185 °F) for all constructions |
Sales Info
Repairable | REPAIRABLE |
Preferred Availability | false |
Quick Turnaround | false |
Dimension Height | 66.04 |
Lead Time | 15 |
Dimension Width | 114.3 |
Dimension Length | 58.42 |
Stock Status | NON_STOCKED |
Weight | 213.188 |
Weight Unit | KG |
Dimension Unit | CM |
Type | Resource | Publication |
---|---|---|
Installation Instructions | 20l-in003_-en-e | 20L-IN003 |
Technical Data | 20l-td001_-en-p | 20L-TD001 |
Technical Data | 20l-td001_-en-p | 20L-TD001 |
User Manual | 20l-um001_-en-p | 20L-UM001 |
Looking for more documentation?
Find curated technical documentation for this product in the Technical Documentation Center, or search our full Literature Library.
Search the Literature Library
Sign in to your Rockwell Automation account to view Knowledgebase Articles.
Sign In
Looking for more Technotes?
Find questions and answers from Rockwell Automation technical experts for this product in our Knowledgebase.
Search Knowledgebase
Technical Specifications
Coolant | Water |
---|---|
Equipment Type | Complete Regenerative Drive |
Feedback Options | Standard Encoder |
Product Family | PowerFlex 700L AC Drive |
Width | 423.8 mm |
---|---|
Height | 955.7 mm |
Depth | 566.1 mm |
Weight | 186 kg |
Terminal bolt size | M8, PE, motor ground bus bar for power terminal |
Custom option | None |
Recommended tightening torque | 40 Nm (354 in-lb)(±10%), PE, motor ground bus bar for power terminal |
SHLD terminal | Terminating point for control wiring shields on the drive for control terminal |
DC bus test point socket | 4 mm socket for DC bus voltage measurement only (2 terminals: DC+, DC-) |
Motor lead lengths | 76 m (250 ft) total |
Wire strip length for active converter cassette terminal blocks-P1 & P2 | 8 mm (0.31 in) for control terminal |
Wire strip length for terminal block-TB1 | 8 mm (0.31 in) for control terminal |
Wire strip length for SHLD terminal | 10 mm (0.39 in) for control terminal |
Wire strip length for PS- and PS+ terminal | 10 mm (0.39 in) for control terminal |
Terminal block-TB1 1b 7: +24V (digin) | Drive-supplied +24V DC for control terminal |
Recommended tightening torque for active converter cassette terminal blocks-P1 & P2 | 0.8 Nm (7 in-lb)(±10%) for control terminal |
Recommended tightening torque for terminal block-TB1 | 0.9 Nm (8 in-lb)(±10%) for control terminal |
Recommended tightening torque for SHLD terminal | 1.4 Nm (12 in-lb)(±10%) for control terminal |
Recommended tightening torque for PS- and PS+ terminal | 0.6 Nm (5.3 in-lb)(±10%) for control terminal |
PS- terminal and PS+ terminal | 300V DC auxiliary control voltage for control terminal |
Wire size for terminal block-TB1 | 0.2 mm² to 4 mm² (#24 AWG to #10 AWG) for control terminal |
Wire size for PS- and PS+ terminal | 0.5 mm² to 4 mm² (#22 AWG to #12 AWG) for control terminal |
Wire size for active converter cassette terminal blocks-P1 & P2 | 0.3 mm² to 3.3 mm² (#22 AWG to #12 AWG) for control terminal |
Wire size for SHLD terminal | 0.3 mm² to 2.1 mm² (#22 AWG to #14 AWG) for control terminal |
Active converter cassette terminal blocks-P1 & P2 | Active converter AC power and control wiring for control terminal |
PE, motor ground bus bar | Terminating point for wiring shields and grounds for power terminal |
Terminal block-TB1 1b 8: gate enable | Enables the firing of the IGBTs. Factory-installed jumper from terminal 1b 7 to terminal 1b 8 allows firing of the IGBTs for control terminal |
Terminal block-TB1 1b 5: +12/+24V cooling loop 1b 6: cooling loop return | Drive control wiring: output dry contact (12V DC/24V DC @ 2A max.) indicating the drive is powered and has completed precharge for control terminal |
Degree of protection (IP) | IP00 |
---|---|
Shock | 10 G peak for 11 ms duration (±1.0 ms), three shocks in each direction, in each axis |
PWM frequency | 4 kHz |
Vibration | 2 mm (0.07 in.) displacement, 1 G peak Alitude, 1 mm (0.04 in.) displacement from 2…13.2 Hz, 0.7 G acceleration at 13.2 Hz to 1.0 G acceleration at 55 Hz, 1 G acceleration from 55 …512 Hz Duration: ten logarithmic sine sweep cycles per axis, at sweep ra |
Number of analogue outputs | 2 None |
---|---|
Mains voltage | 400 V |
DC bus undervoltage shutoff/fault | 300V @ 400V |
DC bus overvoltage trip | 815V @ 400V |
DC nominal bus voltage | 600V @ 400V |
Brake IGBT | No brake IGBT |
Input voltage | 400V AC, 3-phase, 60 Hz |
Torque regulation without feedback | ±5%, 600 rad/sec bandwidth |
Torque regulation with feedback | ±2%, 2500 rad/sec bandwidth |
Internal communication module | EtherNet/IP |
AC input undervoltage trip | 340V @ 400V |
Displacement power factor | 0.98 across entire speed range. |
Circuit breaker current rating, max | 900A @ 400V AC, 3-phase, normal duty |
Motor circuit protector current rating, max | 600A @ 400V AC, 3-phase, normal duty |
Non-time delay fuse current rating, min | 500A @ 400V AC, 3-phase, normal duty |
Non-time delay fuse current rating, max | 900A @ 400V AC, 3-phase, normal duty |
Logic control ride-thru | 0.5 s minimum, 2 s typical |
Brake resistor | No internal brake resistor |
Input current rating | 360A @ 400V AC, 3-phase, normal duty |
Documentation | No documentation |
Carrier frequency | 2, 4 or 8 kHz drive rating based on kHz |
Encoder quadrature | 90°, ±27° at 25 °C |
AC input overvoltage trip | 528V @ 400V |
Electronic motor overload protection | Class 10 motor overload protection according to NEC article 430 and motor over-temperature protection according to NEC article 430.126 (A)(2). UL 508C file E59272 |
Dual element time delay fuse current rating | 500-750A @ 400V AC, 3-phase, normal duty |
Heat sink thermistor | Monitored by microprocessor overtemp trip |
Equipment type | Complete regenerative drive |
Stop modes | Multiple progmable stop modes including RA, Coast, DC-brake, RA-to-hold and S-curve. |
Human interface module | No HIM (blank plate inserted) |
Acceleration/deceleration | Two independently progmable accel and decel times. Each time can be progmed from 0...3600 s in 0.1 s increments |
Frequency accuracy | Digital input: within ±0.01% of set output frequency |
Number of digital inputs | 6 None |
Number of digital outputs | 3 None |
Number of analogue inputs | 2 None |
Supporting protocol for DeviceNet | True |
Additional configuration | None |
Application in industrial area permitted | True |
Supporting protocol for EtherNet/IP | True |
Mains frequency | 60 Hz |
Actual short circuit rating | Determined by AIC rating of installed circuit breaker. |
Output current (with 400V AC induction motor) | Normal duty: 540 A @ 150% of continuous current for 3 s |
Watt loss | Complete drive: 7900 W @ 400V total liquid |
Feedback option | Standard encoder ftdback for enhanced control, vector control |
Enclosure type | IP00/NEMA/UL Type open |
Output current rating | 360A @ 268Hp (200 kW) normal duty, 200 Hp (150 kW) heavy duty, frame 2 |
Control options | 700 vector control with 24V DC I/O |
Drive overcurrent trip | Software overcurrent trip: 200% of rated current (typical) |
Efficiency | 96.2% at rated A, nominal line volts |
Encoder supply | 12V @ 250mA. 12V @ 10mA minimum inputs isolated with differential transmitter, 250 kHz maximum |
Output frequency | 0 to 420 Hz |
Speed control | Speed regulation with ftdback: 0.001% of base speed across 120:1 speed range 1000:1 operating range 250 rad/sec bandwidth |
Current limit capability | Proactive current limit progmable from 20...160% of rated output current, Independently progmable proportional and integral gain |
Selectable motor control | Sensorless vector with full tuning. Standard V/Hz with full custom capability and vector control with force technology (with and without ftdback). |
Frequency control | Speed regulation with slip compensation (volts per Hz mode): 0.5% of base speed across 40:1 speed range 40:1 operating range 10 rad/sec bandwidth |
Input phases | 3-phase input provides full rating for all drives. |
Control method | Sine coded PWM with progmable carrier frequency |
Encoder requirements | Encoders must be line driver type, quadrature (dual channel) or pulse (single channel), 8...15V DC output (3.5...6V DC @ 5V encoder), single-ended or differential and capable of supplying a minimum of 10 mA per channel. Maximum input frequency is 250 kH |
Number of phases output | 3 None |
Number of phases input | 3 None |
With control element | True |
Supporting protocol for TCP/IP | True |
Supporting protocol for PROFIBUS | True |
Supporting protocol for CAN | True |
Supporting protocol for Modbus | True |
Application in domestic- and commercial area permitted | True |
Encoder duty cycle | 50% ±10% |
Input frequency tolerance | 47...63 Hz |
Input frequency, ,max | 400 kHz ftdback |
Output voltage range | 0 to rated motor voltage |
Encoder type | Incremental, dual channel |
Short circuit trip | Phase-to-phase on drive output |
Ground fault trip | Phase-to-ground on drive output |
Control logic noise immunity | Showering arc transients upto 1500V peak |
Line transients | Up to 6000 volts peak per IEEE C62.41-1991 |
Output power bus bar | Motor connections (U/T1, V/T2, W/T3) for power terminal |
Input power bus bar | Input power connection (R/L1, S/L2, T/L3) for power terminal |
Intermittent overload | 110% overload capability for up to 1 min, 150% overload capability for up to 3 s |
Short circuit current rating | To match specified circuit breaker capability, less than or equal to 200000 A symmetrical. |
Encoder input voltage supply | Dual channel plus marker, isolated with differential transmitter output (line drive) incremental, dual channel quadrature type 5V DC or 12V DC (5V DC requires an external power supply), 320 mA/channel for ftdback |
Pressure drop from drive inlet to drive outlet at minimum coolant flow rate | 1.58 bar |
---|---|
Estimated amount of coolant | 15.1 L |
Coolant temperature | 0 °C |
Altitude | 1000 m (3280 ft) at rated current |
Surrounding air temperature without derating, max | 0 to 50 °C (32 to 122 °F) @ IP20, NEMA/UL Type 1 |
Coolant type | WEG50 equals good quality or distilled water with approved inhibited ethylene glycol, 50% glycol by volume or WPG50 equals good quality or distilled water with approved inhibited propylene glycol, 50% glycol by volume. |
Atmosphere | Drive must not be installed in an area where the ambient atmosphere contains volatile or corrosive gas, vapors, or dust, If the drive is not going to be installed for a period of time, it must be stored in an area where it will not be exposed to a corrosi |
Coolant flow rating | 30.3 l/min |
Relative humidity | 5...95% noncondensing |
Storage temperature | -40...85 °C (-40...185 °F) for all constructions |
Sales Info
Repairable | REPAIRABLE |
Preferred Availability | false |
Quick Turnaround | false |
Dimension Height | 66.04 |
Lead Time | 15 |
Dimension Width | 114.3 |
Dimension Length | 58.42 |
Stock Status | NON_STOCKED |
Weight | 213.188 |
Weight Unit | KG |
Dimension Unit | CM |
Documents
20l-in003_-en-e
Installation Instructions
20L-IN003 |
20l-td001_-en-p
Technical Data
20L-TD001 |
20l-td001_-en-p
Technical Data
20L-TD001 |
20l-um001_-en-p
User Manual
20L-UM001 |
Type | Resource | Publication |
---|---|---|
Installation Instructions | 20l-in003_-en-e | 20L-IN003 |
Technical Data | 20l-td001_-en-p | 20L-TD001 |
Technical Data | 20l-td001_-en-p | 20L-TD001 |
User Manual | 20l-um001_-en-p | 20L-UM001 |
Looking for more documentation?
Find curated technical documentation for this product in the Technical Documentation Center, or search our full Literature Library.
Search the Literature Library
Technotes
Sign in to your Rockwell Automation account to view Knowledgebase Articles.
Sign In
Looking for more Technotes?
Find questions and answers from Rockwell Automation technical experts for this product in our Knowledgebase.
Search Knowledgebase
Find a sales and technology partner
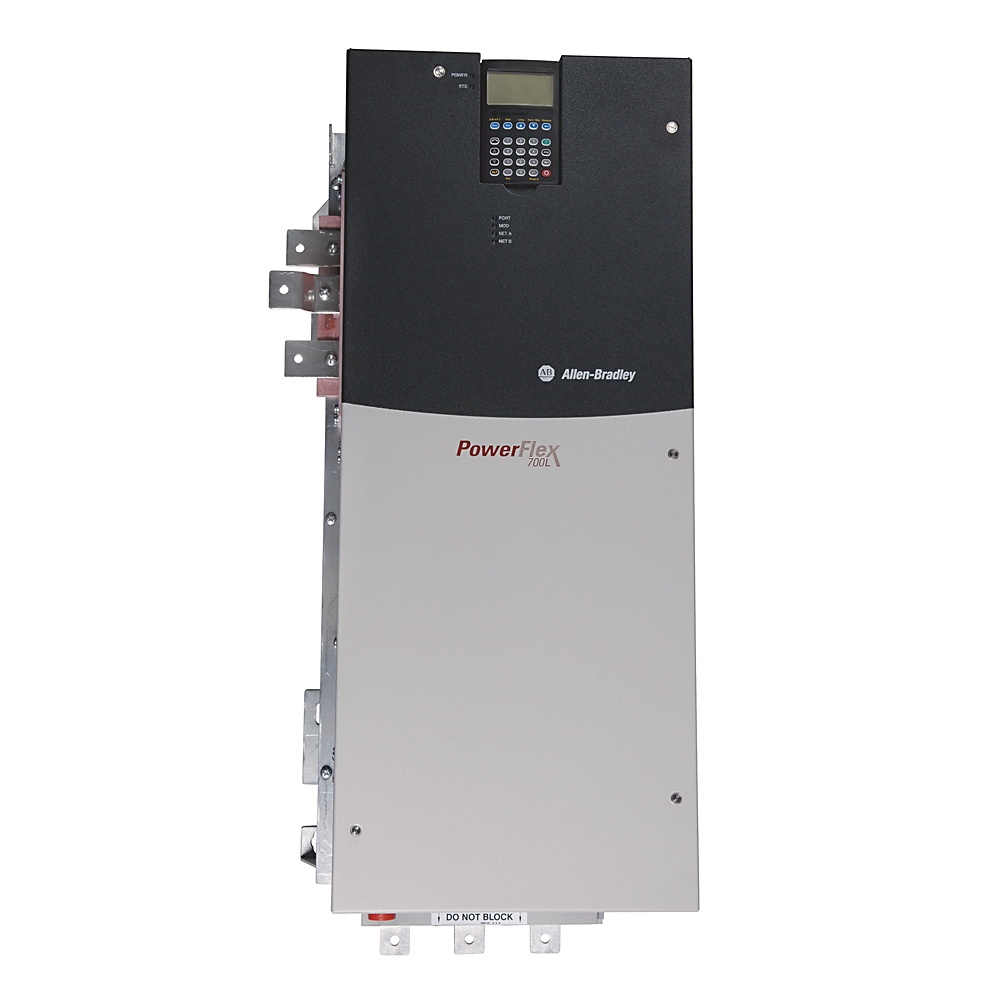
Copyright ©2024 Rockwell Automation, Inc.