Downloads
What is this for?
The "Energy Saving Monitoring System with FactoryTalk Optix" developed in FactoryTalk Optix aims to provide a clear and understandable visualization of energy efficiencies by allowing operators to monitor tank levels, flow rates in pipes, and other critical parameters in the extraction and pumping process in a beverage industry; thus, facilitating faster decision-making and problem resolution.
Additionally, integration with FactoryTalk Optix enables effective alarm management. Operators can configure alerts for critical events, such as tank level deviations or equipment failures, ensuring timely intervention and minimizing downtime. This way, we can ensure:
- Reducing losses
- Increasing asset utilization
- Maintaining optimal quality levels
- Real-time data collection
- Improving the use of energy resources (WAGES: water, air, gas, electricity, and steam)
Characteristics
“Energy Saving Monitoring System with FactoryTalk Optix" offers the following features:
- Connectivity between information stored in the controllers for processes
- Remote activation and control of motors
- Collection and analysis of data, providing information on process performance and efficiency
- Efficient alarm management
Advantages
- Enhanced decision-making: by visually presenting real-time data and information through FactoryTalk Optix, the demonstration enables users to make informed decisions regarding process optimization, resource allocation, and equipment maintenance.
- Cost-saving visualization: the “savings” screen, powered by the VFD PowerFlex 520 series, demonstrates potential cost savings associated with the implementation of these technologies. Users can see tangible evidence of how investing in automation can generate financial benefits over time.
- Safety and reliability: the “Alarms” screen highlights the importance of proactive monitoring for safety and reliability in the extraction process. Users can appreciate the value of early detection and response to potential issues, minimizing downtime and ensuring consistent product quality.
Is it useful for me?
The growing demand to achieve "net zero” carbon emissions require technologies that allow us to monitor the energy consumption of motors in plants and; if it is an application where torque is variable, as it is the case with pumps, take small actions that allow consume less water and energy. Thus, through the PowerFlex 520 family, manufacturers will be able to improve the performance and overall efficiency of the equipment (OEE).
Customer demand is versatile and presents different scenarios in production lines. Manufacturers will have to implement flexible and reconfigurable automation to address energy consumption challenges. Through this project, a Studio 5000 program simulates the water demand required by the industry, and Optix allows users to become aware of the savings that the drive provides.
How can I make it work?
Hardware:
- PowerFlex 525
Software:
- Studio 5000 (v33-35)
- FactoryTalk Optix (v1.2.0.272)
- CompactLogix 5370
Knowledge required:
Familiarity with modifying parameters of frequency drives of the 520 family A-B and knowledge of the CompactLogix 5370 family.
Please note: You will need to agree to the Terms & Conditions for each download.
Need help?
If you need help with an application or have feedback from the Innovation Center, please contact us.
Installation Guide
Step 1:
Familiarization with the Program.
Note that in the left panel "Controller Organizer," there are 4 routines. In BATCH_CONTROLS, can be found the control of system power on/off and motors power on/off. In the "FILLING ROUTINE", the filling process of a tank is simulated, while in the "EXTRACTING ROUTINE," the tank extraction is simulated. The "FLOW_METERS" routine simulates how the water flow increases as more time is spent pumping.
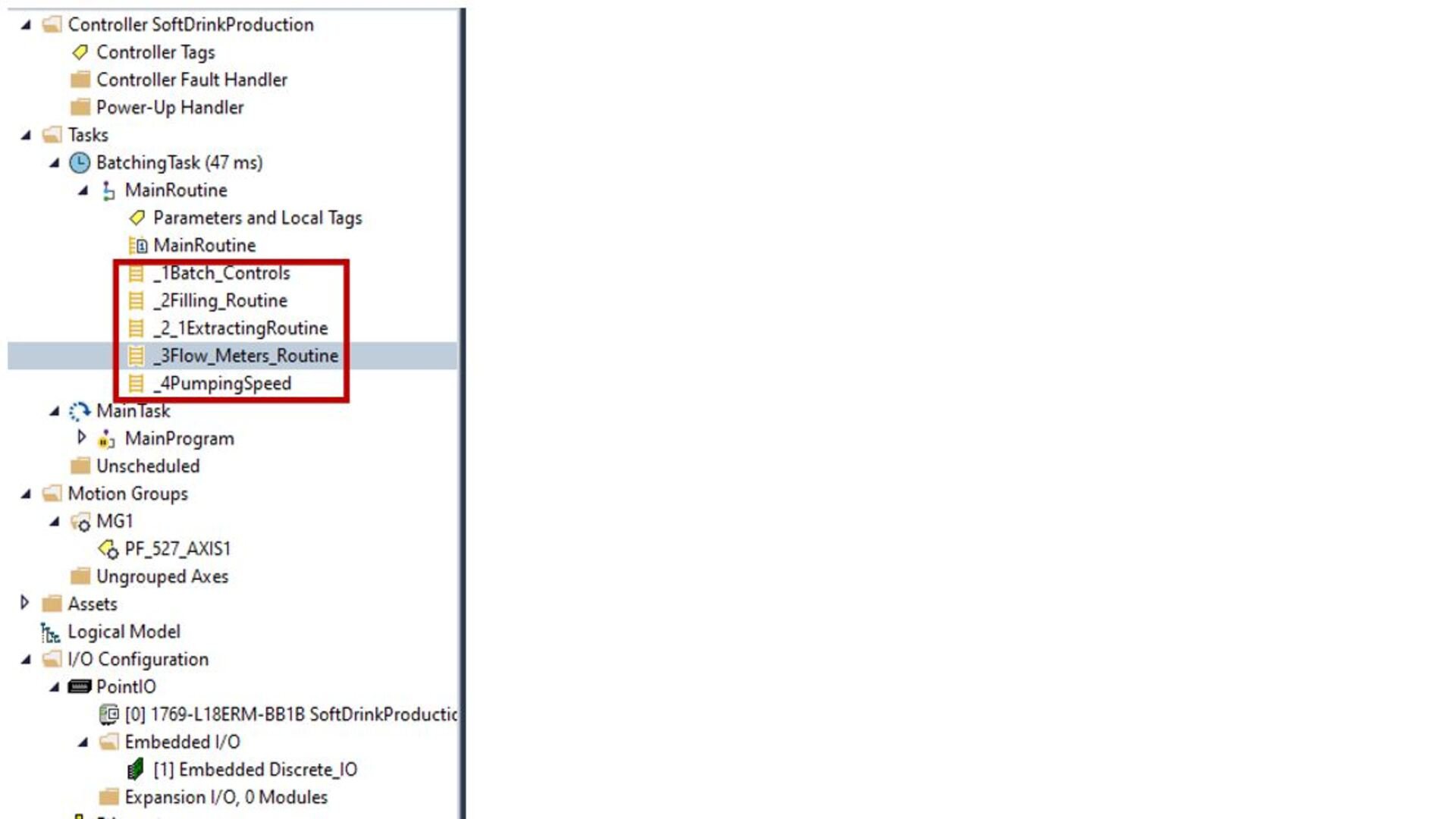
Step 2
Verify that the SoftDrinkProduction program has been downloaded into the controller and is already online.
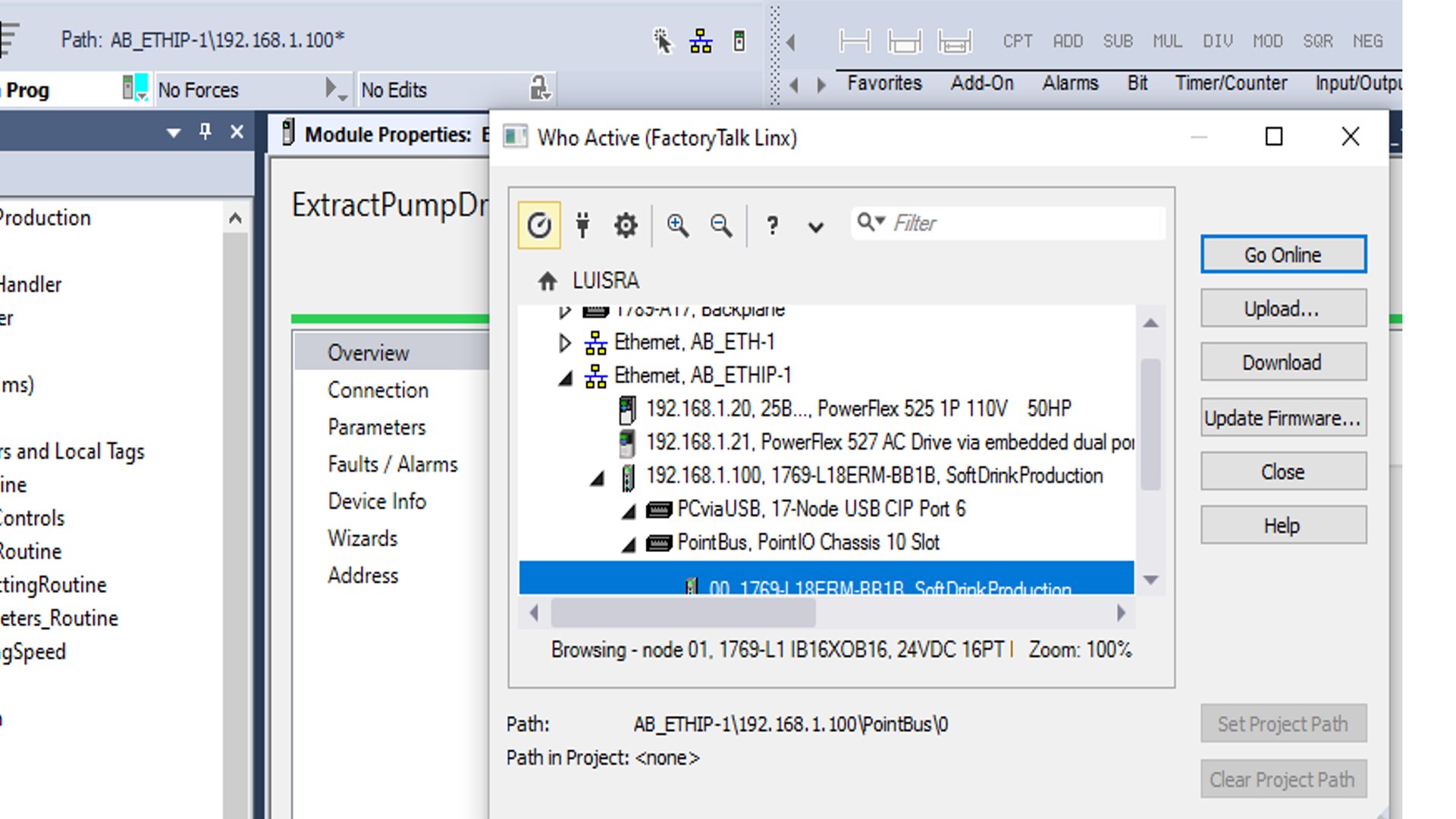
Step 3:
Familiarize yourself with the PowerFlex 525, that is, which parameter it starts, stops, and which one changes the speed. Note that the PowerFlex is active and running.
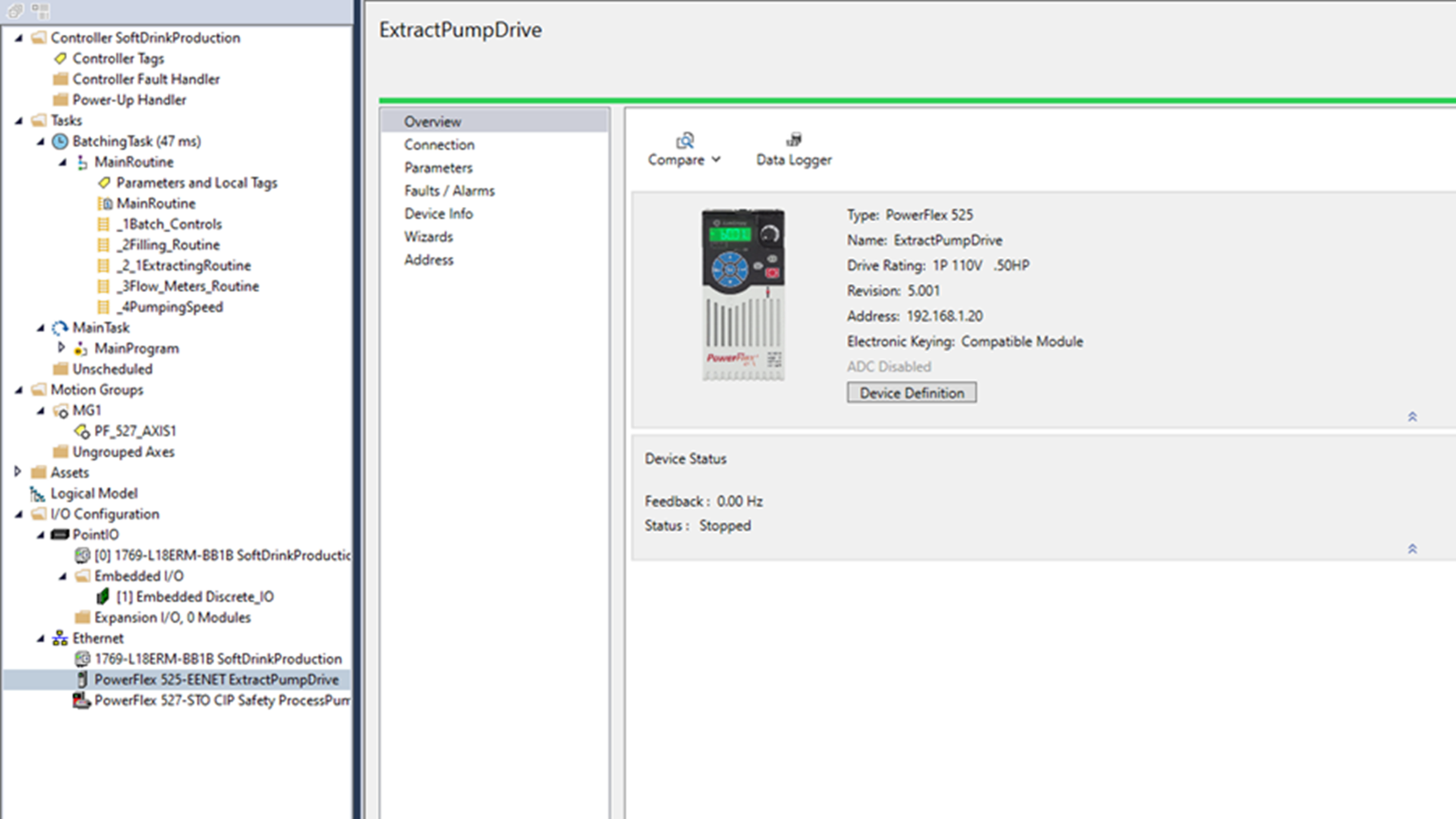
Step 4
Open the Factory Talk Optix program.
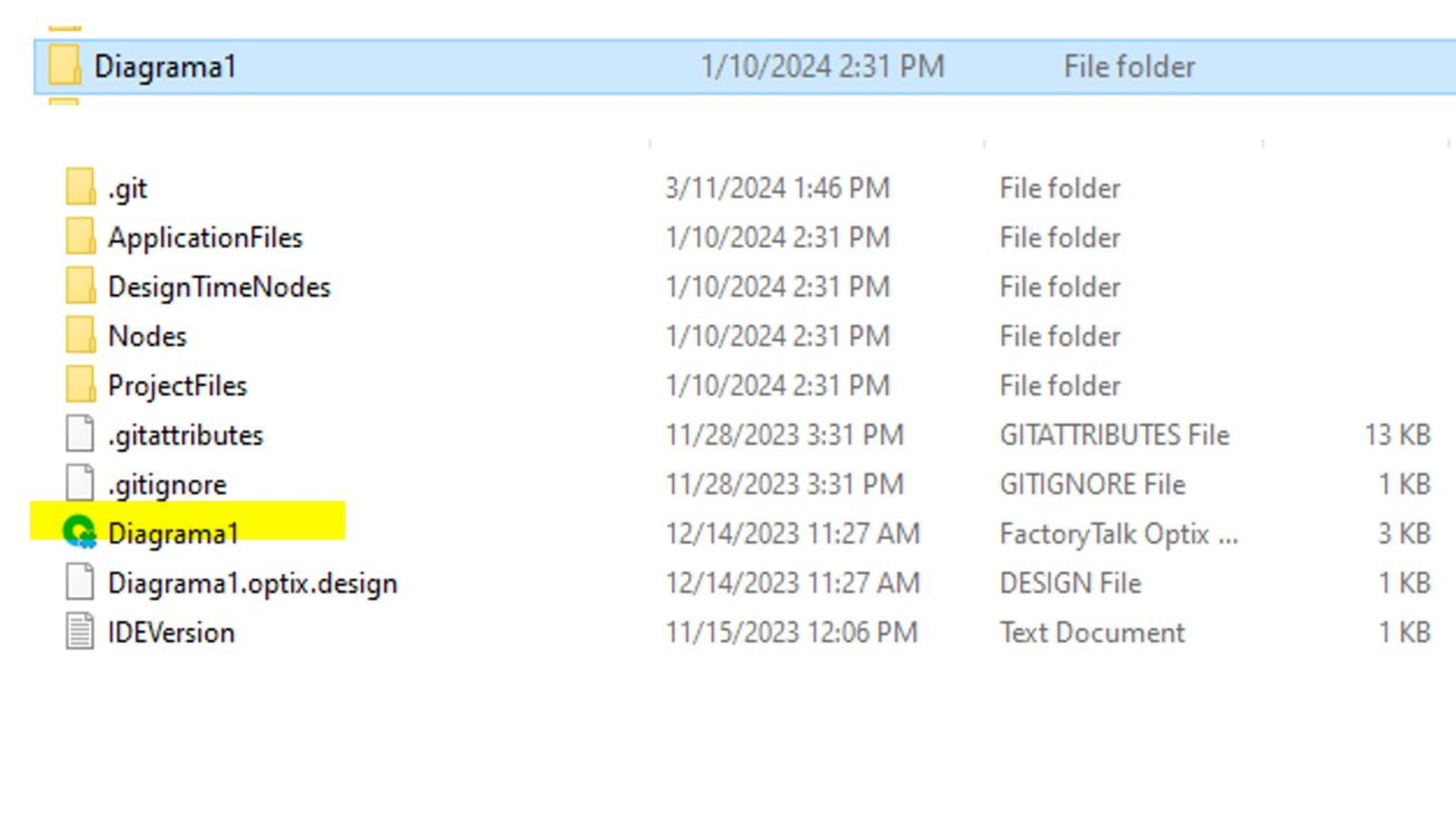
Step 5
Verify that the controller is already on the correct BackPlane on FactoryTalk Optix.
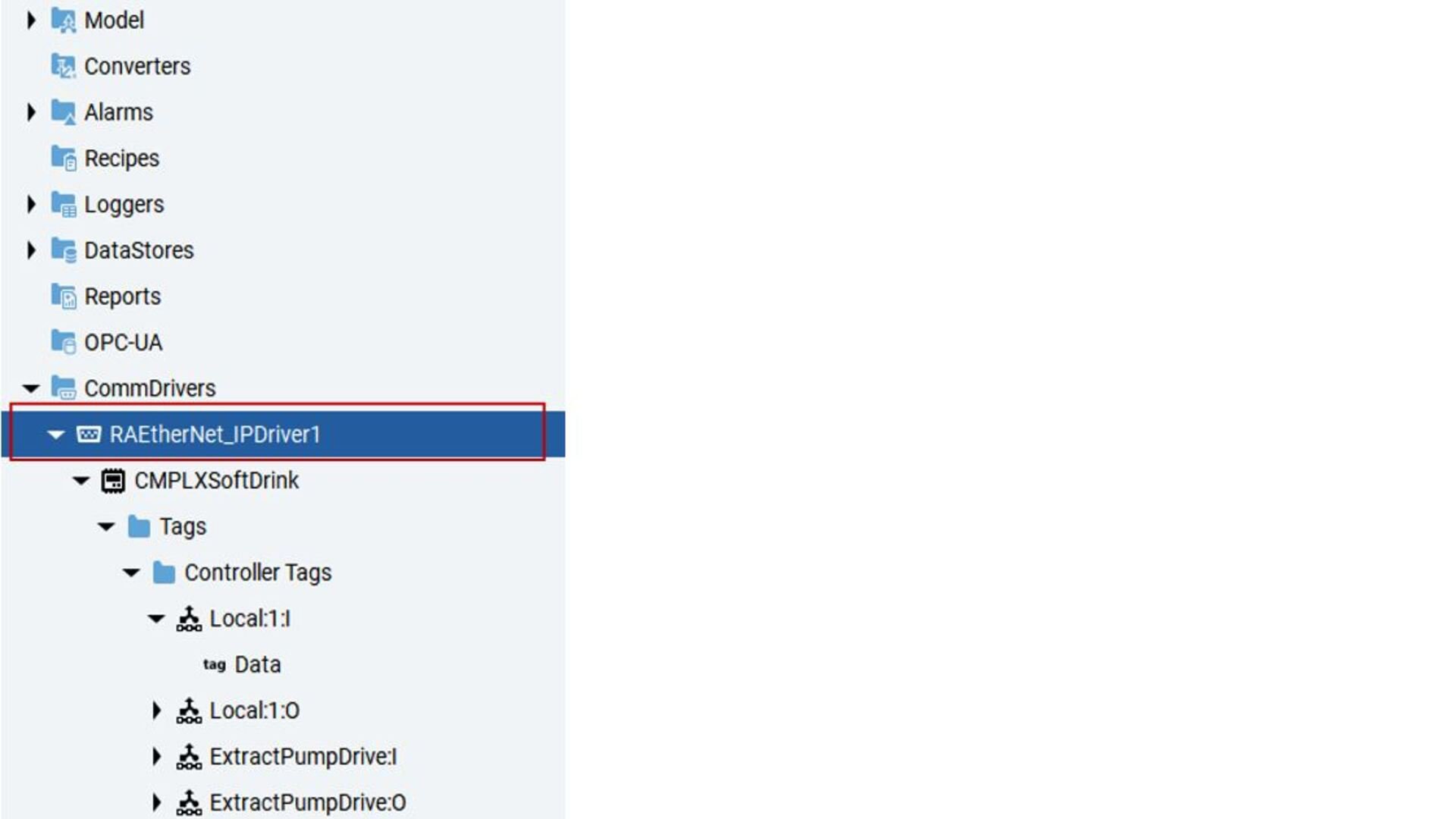
Step 6
Run the program from the main toolbar located at the top of the interface.
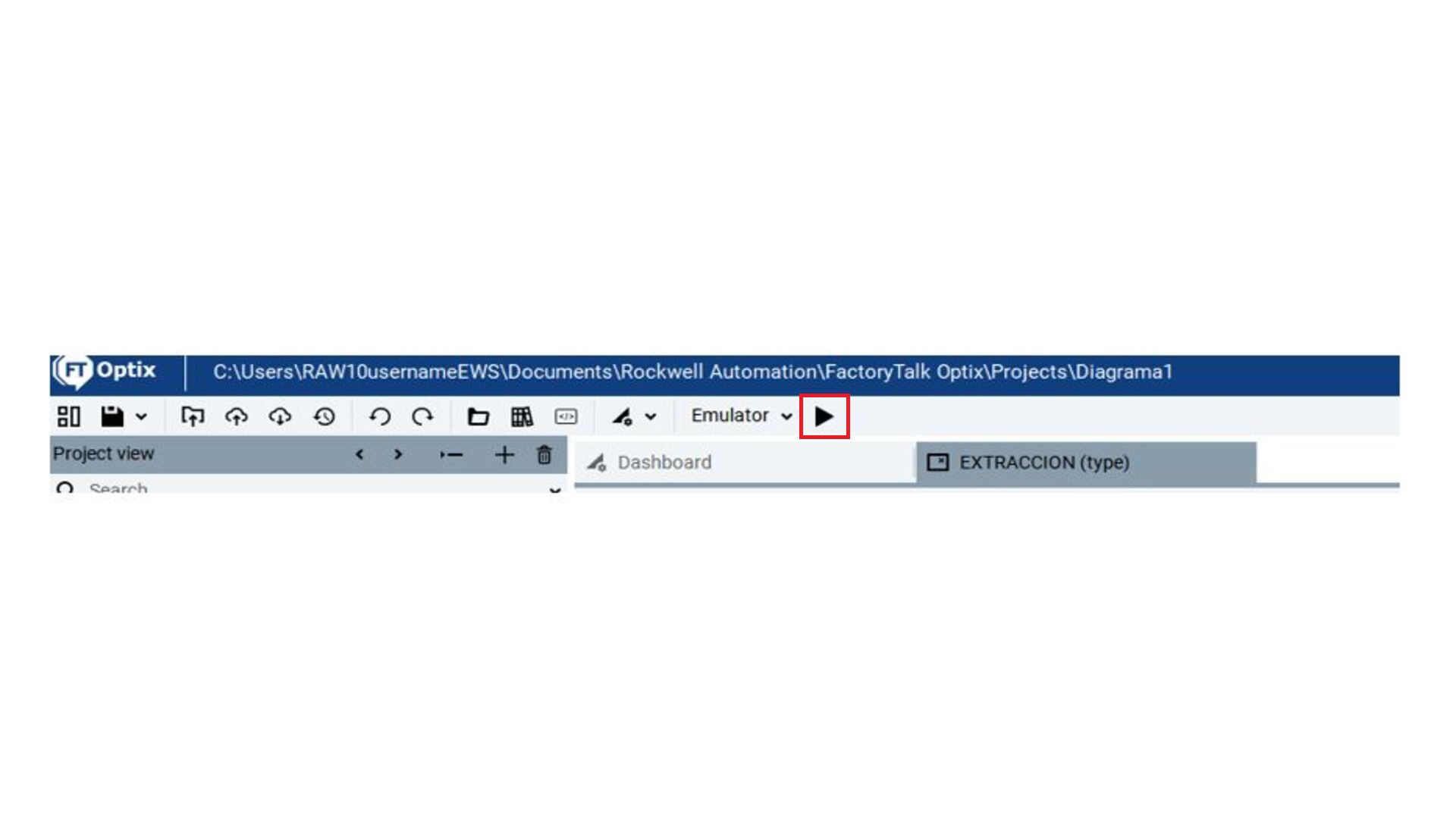
Step 7
7.1 Once the program is running, the main screen will be displayed where you can observe:
- The tank level.
- If there is a flow difference (you can simulate a flow difference by pressing the "Resolved Difference" button).
- The buttons that start and stop the extraction process.
- And the alarms that notify if there is a flow difference in the pumping process compared to the suction process (at the top of the "Extraction" screen).
The navigation bar is located at the bottom.
Extraction Screen: Allows monitoring the extraction process from a well to notify the operator if a pipe leak occurs.
7.2. Process Control Screen: Here, the extraction process from a tank can be visualized.
At the beginning, a warning screen will appear informing us that the production for the beverage industry in this example ranges from 200 bottles per minute (BPM) to 480 BPM.
7.3. On this screen, on the left, you can reset the parameters of the "Extraction" and "Process Control" screens (parameters such as tank level, pumping and extraction flows, the number of bottles entered, etc.). In the textbox on the right, you can enter the number of bottles required for production and observe how the revolutions per minute (RPMs) change on the motor's faceplate.
- To access the faceplate of the motor on the right, click on the motor.
- To start or stop the motor, simply click on START and STOP respectively.
- If you want to close the faceplate, click on the X in the bottom left corner.
- It is worth noting that if you do not enter a number of bottles per minute [BPM], i.e., 0 or less than 200 BPM, you will see that the extraction process is carried out in "active saving" mode (automatic), meaning the motor speed is self-negotiated between the pumping flow and what is extracted to satisfy a tank level greater than 50%, i.e., to prevent the pump from running out of water.
- If you enter a BPM number, the motor speed will vary; and in the process simulation, developed in Studio 5000, it was done in such a way that if you enter a number higher than 350 BPM, the pump will extract more liters than the liters that are being filled. However, if the tank level drops below 20%, the motor will automatically shut off.
7.4. Alarm Screen: This screen allows monitoring all system alarms, as well as important trends such as tank level, pump speed, and pumping flow in gallons per minute [GPM].
7.5. Data Screen: Allows recording tank level data, as well as detecting leaks in the water extraction process from the well into the tank.
7.6. Savings Screen: In this screen, you can observe how by varying the motor intensity, based on the affinity laws of centrifugal pumps, greater energy savings are achieved compared to controlling the flow with a throttling valve.