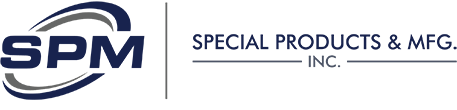
Special Products & Mfg., Inc. has been serving OEMs for over 50 years, specializing in metal fabrication, contract manufacturing, welding, and more. A premier ISO 9001:2015 certified company, they are committed to driving innovation and redefining what it means to be a modern manufacturing company.
- Undocumented knowledge
- Manual processes for scheduling and data entry
- Time-consuming reporting
- 30% reduction in inventory levels
- 30-40% reduction in expedited freight
- 75% increase in revenue per FTE
- Ability to scale without additional headcount
- 100% data accuracy
Challenge
Modernizing Business Operations
Always looking for ways to modernize their business, Special Products & Mfg. Inc. (SPM) knew that many of their internal and operational processes needed to be updated. For example, the workforce was relying on company knowledge that was based largely on memory. This made it difficult to systemize that knowledge, document it formally, and make it accessible to everyone. The memory-based knowledge was also making it difficult to add new knowledge and best practices that would help the company grow.
Additionally, SPM was running on manual processes for scheduling shifts, reporting quality issues, and extracting reports—all tasks that were vulnerable to human error. For example, non-conformance issues would be recorded on hand-written pieces of paper, delivered to the management team, and two or three days later, make their way to critical downstream departments.
Finally, SPM was challenged by reports that were difficult to extract from their current system and that had unreliable accuracy. Staff would have to take time to pull data from one portal and manually type it into an ERP. SPM was not able to forecast which and how many parts they would need in the coming months, leaving them to scramble to fill customer orders while dealing with each part’s varying lead time.
On the Hunt for an MES Solution—More Efficiency, Reliability, and Connectivity
SPM needed streamlined processes, better access to reliable data, and more connectivity between departments. As a company that walks its talk, the team searched for an MES solution to help them modernize this part of their business once and for all.
When SPM found the Plex MES solution, they knew they found a platform designed exactly for their needs. They were looking to eliminate manual work prone to human error, connect departments to one another, and ensure 100% data accuracy. Specifically, SPM implemented three core Plex solutions: MES, Quality Management, and Production Monitoring.
Solution
MES
SPM sought to eliminate the reliance on memory-based knowledge and the challenges associated with systemizing, documenting, and making knowledge accessible to all employees. The Plex MES solution played a pivotal role in streamlining this aspect. By providing a centralized platform for managing production activities in real-time, the MES solution allowed SPM to digitize and organize crucial information, breaking free from memory-bound processes. The system facilitated seamless coordination between different teams, ensuring that everyone had access to up-to-date and standardized knowledge.
Quality Management
“The cost of quality has been a big focus for our strategic plan,” says Nora Harding, Executive Vice President at SPM. Nora and her team knew that Plex's Quality Management module would empower them to shift from manual processes for recording non-conformance to a digitized, automated system. This not only enhanced accuracy but also accelerated the identification and resolution of quality issues. Real-time visibility into quality metrics allowed SPM to proactively address concerns, fostering a culture of continuous improvement.
Production Monitoring
“We used to have one system that was operationally focused. It did not have great reporting or metrics that we could get from it,” says Nora. That’s why the SPM team also chose to implement the Plex Production Monitoring tool. This module offered real-time insights into production activities, enabling swift and accurate reporting. The system's ability to extract and present data in a user-friendly format eliminated the need for manual data entry, reducing the risk of errors. Production Monitoring also empowered SPM to forecast part requirements more accurately, optimizing inventory management and ensuring timely fulfillment of customer orders.
Result
Product Quality
From a product quality perspective, the Plex Quality Management module has been amazing for SPM. Reporting non-conformance issues used to take days to trickle down to critical departments. With Quality Management, all quality data is electronically in the system with 100% accuracy and accessibility to everyone. During an audit, managers can pull reports with reliable data on a moment’s notice, which has helped improve SPM’s Cost of Quality. Plex has also helped SPM improve their company culture. Armed with data, associates can pose informed questions to managers and provide recommendations.
Shop Floor Operations
Plex has transformed shop floor operations at SPM. Since implementation, SPM saw a 75% increase in revenue per FTE. Before Plex, scheduling was a very manual process. Since implementation, supervisors use the hot list to make adjustments before and during shifts to make sure associates have what they need at any time. Supervisors can pull data easily to see a 10-min look at what they need to know for the rest of the day to make sure everything is on track. It also helps supervisors ensure that any automated work was completed successfully the night before.
SPM also saw a 30% reduction inventory levels, resulting in lower carrying costs and better cash flow. Plex has allowed SPM to practice just-in-time manufacturing. Whenever a customer places an order, there’s a lead time. As that part goes through the floor, it stops at various departments. With Plex, SPM can pull reports that allow them to forecast and buy to that forecast. The system will drive when they need to purchase those items.
Perhaps most critical to shop floor operations is that previously disparate departments can now collaborate seamlessly. Bo Carroll, Engineering Manager at SPM says, “I’m most excited about the total connectivity that we can have, that kind of connectivity from the front to the back is super exciting and Plex has allowed us to do that.”
Workforce Management
When it comes to cultivating a successful, engaged team of shop associates, “it’s all about having what they need, when they need it,” says Tanya Lance, HR Manager at SPM. Plex has enabled SPM to execute a smooth onboarding process from when associates are hired to when they enter the shop floor. With Plex, SPM can support their associates with great technology in their internal systems, just as they connect them with great technology in their equipment on the shop floor.
Associates get particular use out of the Employee Suggestion module. It allows users to feel heard and build SPM’s culture of employee engagement. While employee engagement has been a longstanding value at SPM, “Plex allowed us to take that to the next level,” says Tanya. More tangibly, Plex’s streamlining of employee processes and maximizing of employee time has given SPM the ability to scale their business without adding headcount.
SPM has always had strong values of innovation, quality, and teamwork. Plex’s MES solution and other tools are helping SPM live out those values in every aspect of the business and achieve tangible results—from product quality to shop floor operations to workforce management.
Published March 1, 2024