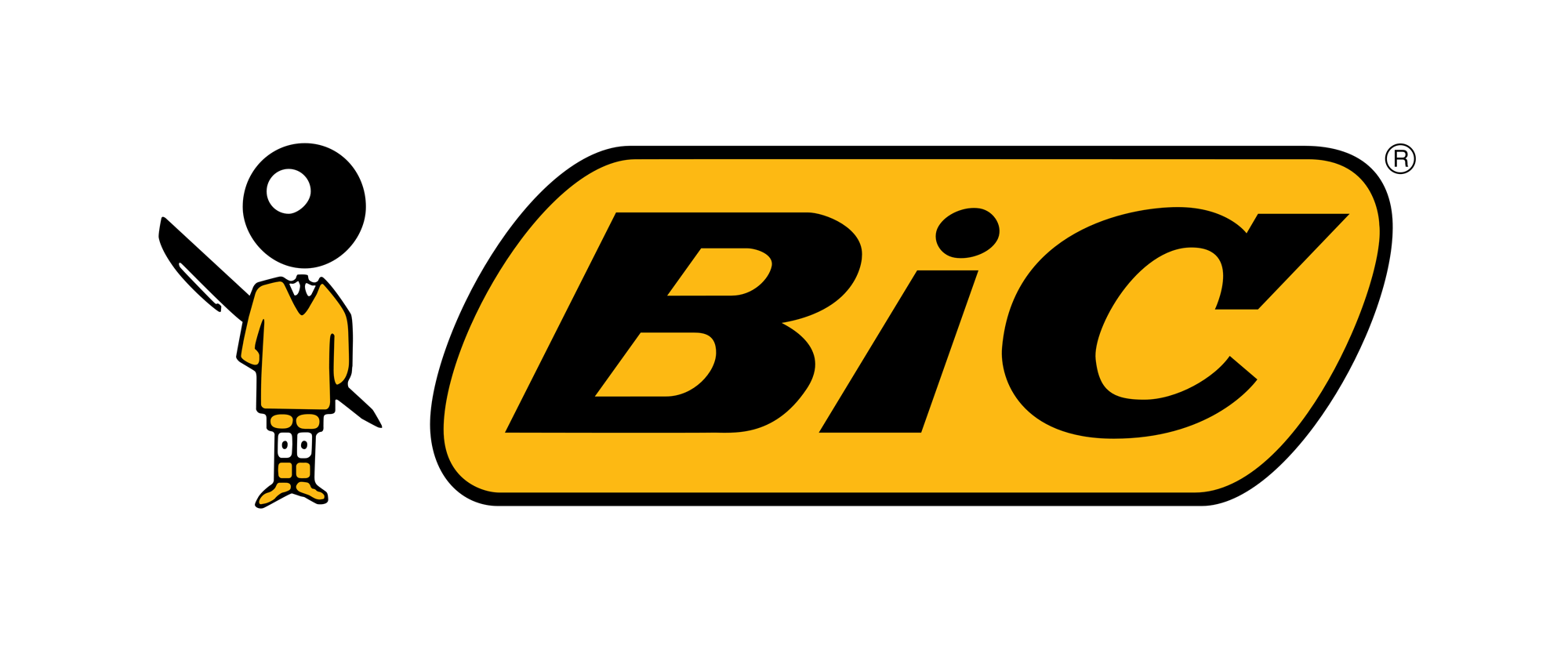
A world leader in stationery, lighters and shavers, BIC brings simplicity and joy to everyday life. For more than 75 years, the company has honored the tradition of providing high-quality, affordable, essential products to consumers everywhere.
- Lack of standardization leading to disjointed production processes
- Disconnected workers operating without unified data sources
- To replace paper-based systems with a standardized cloud-based solution
- Daily recorded transactions increased to more than 100,000 finished good parts per single shift
- Improvements to overall visibility, shop-floor performance and OEE simultaneously
- Full traceability from raw materials to finished product
Challenge
Real-time visibility into production processes, inventory levels, and quality metrics is now an essential requirement to remain competitive in modern manufacturing, even for established, iconic brands. Manufacturing giant BIC, a world leader in stationery, lighters, and shavers, wanted to embrace the possibilities that digital transformation offers for operational efficiency.
BIC signed a multi-site Manufacturing Execution System (MES) subscription agreement with Plex and Rockwell Automation in December 2020 for a comprehensive suite of tools to manage and optimize manufacturing operations from shop floor to top floor. The initial pilot project was focused on BIC’s manufacturing facility in Bizerte, Tunisia, which serves as one of the primary stationery production plants for the Europe, Middle East, and Africa (EMEA) regions.
Laying the foundation for seamless integration
As with any transformative project, there were several key challenges BIC was looking to overcome. The main one the company faced in this instance was the standardization of all their production processes. However, this needed to be achieved alongside both horizontal and vertical integration, combining machines and workers on a larger scale than was currently possible with existing ways of operating.
According to Rogelio Demay, Senior Manager Information Technology, EMEA at BIC: “BIC’s journey towards digital transformation was always fundamentally about integrating people and technology to improve operations.”
Here, for BIC, the goal was to break operational silos and connect workers more effectively through unified data sources that could help improve and optimize operations in Bizerte. Then, once validated, this blueprint for success could be scaled to more of the company’s facilities over time.
By focusing on standardizing systems, Demay believes that the Bizerte project is a key part of BIC’s ongoing journey towards digital transformation and operational capability enhancement. For this approach to be successful, the focus must be worker-centric. He states: “We continuously build on the strong manufacturing foundation that we pride ourselves with. Our latest project is testament to our innovative mindset and adoption of technology to enhance operational efficiency. Integrating MES within the day-to-day operations to support our people, the main reason for success, will help us go a long way.”
Solution
Integration through simplification
One of BIC’s key objectives was to replace local bespoke solutions with a standardized cloud-based system that could be accessed from any location. BIC selected Plex MES to support a company-wide smart manufacturing initiative targeted to simplify and synchronize manufacturing tools, standards, and processes globally.
However, to move forward, first BIC had to look back. This was crucial to generating lasting success, as Dafni Vakasi, Smart Manufacturing Manager at BIC, understood when the project was first kicking off. She explains: “The first step of the project was to go onto the shop floor and really understand the way the factory operates. Having a fundamental understanding of what an operator was doing, what they were looking at, and what information they needed, was vital to ensure we can get it to them efficiently.”
With Rockwell Automation’s Plex MES, BIC was able to transition from several fragmented pieces of software, some of which had been developed in house, to a fully integrated execution system. This alleviated the issue of many factories working with different software, servers, and operating systems, each of which yielded different levels of quality.
By simplifying the overall IT footprint, BIC achieved two things. Firstly, they now had one single MES solution that could drive most of the functions in the factory. Secondly, they were able to resolve the operational silos that caused some inefficiencies. This enabled the users to leverage the power of advanced machinery, share reliable information, and work with the same, accurate data.
Vakasi explains the benefits of this approach being that BIC now had full visibility over their entire operations. “We're really discovering the way we do things, the way we document everything, which is great because it means we can find the right solutions that will directly benefit all our operators,” she said.
Result
Making improvements on a global scale
The BIC Plex MES solution covered end-to-end processes including 90 molding and assembly lines with various automation levels. Despite the plant’s scale and complexity, BIC achieved deployment of the MES Advance package out of the box and were able to improve shop-floor processes. During the initial go-live week, even with reduced production, daily recorded transactions saw thousands of produced containers, increasing to more than 100,000 finished good parts per single shift.
The core benefits they realized centered on improving overall visibility to shop-floor performance and OEE with MES and MACH2 A&O, as well as a significant increase in inventory accuracy, which in turn helped to improve production planning. As a result, BIC could now ensure full traceability from raw materials to the finished products, as well as for shipping and beyond.
Demay praised the pilot project, saying: “The shift from a paper-based system to Plex MES has been a tremendous step towards self-sufficiency. It has enabled us to react swiftly to issues and drive continuous improvement.”
With the Plex MES solution helping connect machines and resolve silos, the next step for BIC is to take this successful approach and apply it to additional facilities around the world, connecting their entire global operations under one standardized approach. Rockwell Automation has also been a key partner in this initiative, supporting BIC's vision to connect operational technologies and the IoT world, bridging the gap between these two spheres and seamlessly integrating them into the company's operations.
Over the course of the entire project, BIC and Rockwell Automation have worked together closely, through the implementation of the MES combined with the shared desire to push each other to generate significant improvements. With evident success, this project is just the beginning for BIC as the company progresses on its digital transformation journey and objective of standardizing systems on a global scale.
The success of the BIC Bizerte pilot has opened doors for larger MES/MACH2 roll outs in many different locations, with Vakasi stating: “What really helped us when designing this solution for our facilities is how flexible the Plex solution can be. We sat down with the Rockwell specialists and designed the solution to fit the needs of the Bizerte team. This approach can be applied to our factories in the rest of the world as well, such as Athens, Manaus, and even looking into Mexico. This is our journey towards smart manufacturing, and Rockwell Automation will be a major part of it.”
Published January 3, 2024