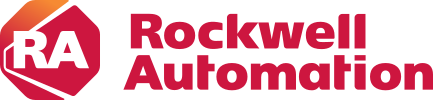
Global toy company commits to plastic-free packaging and calls upon leading machine builder to help solve packaging and material challenges.
A Rockwell Automation solution was installed, which included:
- Allen-Bradley® Compact GuardLogix® Programmable Automation Controllers
- Allen-Bradley Kinetix® 5500 Servo drives
- Allen-Bradley PowerFlex® 525 variable-speed drives
- Stratix™ 2500 Ethernet switches
- Allen-Bradley PanelView™ +7 HMIs
- 95% paper-based alternative successfully developed
- Patent filed for 100% paper-based solution
- Existing close R&D cooperation
- Automation solution based on established, industry-proven platform
- End customer already a Rockwell Automation user, so familiarity and integration not a problem
- Global support and supply capabilities
Challenge
Anyone who has helped unbox their kid’s gifts on birthdays will attest to the volume of plastic left behind. Some is recyclable, some, unfortunately, is not. Although eminently suitable for packaging purposes, in its single-use guise, plastic has become a pariah from a sustainability standpoint. It is now the subject of myriad high-profile global actions and programs to reduce and remove it from as many applications as possible.
As a result, virtually every vertical industry is looking at ways to remove or replace single-use plastics with recyclable or compostable variants, or even replace it entirely with more ecologically appropriate materials.
One global toy manufacturer recognized that it needed to take a lead in sustainability and set an example. As a result, it has committed significant research and development efforts into defining sustainability initiatives.
In addition to the plastics used in its products, for which it was already investigating recyclable replacements, the company also needed to consider the materials used in packaging and took the decision to replace the plastic bags with paper, with the ultimate goal of all toy sets being entirely paper bagged by 2025. As a result, the search began to find a company that could supply the necessary expertise and machinery to fulfill these objectives.
“It began when a representative approached our sister company, Fawema, at interpack,” explains Lars Bergerhof, Sales Director of HDG – Verpackungsmaschinen GmbH. “Our experience of filling products into edge-sealed pouches saw us added to a list of 80 potential candidates, from which we were chosen to lead the development efforts.
“We already had experience with paper for products in the food and beverage industry,” Berghof explains, “so the packaging dynamics were not an issue. If anything, they were slightly simpler due to the removal of the inert gas protection needed for foodstuffs. However, existing technologies are based around paper laminated with polyethylene, which although better than 100% plastic, was not the ideal target. We needed to find a solution based on 100% paper.”
Solution
The first paper-based solution currently in operation still requires a thin PE additive (less than 5% of the total material) to support the efficacy of the sealing. But thanks to further development efforts, HDG has addressed the next major step and a global patent for paper bags with zero-percent plastic has been filed. This will use a mechanical pressure seal to create a seam not unlike those on coffee-machine filter papers. This 100% paper solution is currently under approval with the customer and should see deployment in the future.
Result
In operation, the machine takes paper from roll stock and then forms, side seals and cuts it to form a pouch. This empty pouch is then transferred to a filling station where it is checked to see if it is open, before being filled with a pre-selected ‘portion’ of parts. Following this, the pouch is fully sealed before being passed to secondary packaging.
The solution HDG developed for its customer is based around a modified variant of its RB-200/300 horizontal form, fill & seal (HFFS) machine. “Our machines deploy a modular design,” Bergerhof elaborates. “No matter the product shape, we can develop a pouch-based solution. Apart from the material choice, our customer also challenged us to build a machine that would occupy a similar footprint to an existing vertical form, fill and seal (VFFS) variant. It runs several types of formats such as 3- or 4-side seal or stand-up pouch.
Rockwell Automation was selected as the automation supplier for several reasons. First, HDG has experience in using the global automation and information leader’s products with their seamless integration, even those in prototype form; second, the customer already had several Rockwell Automation-based solutions in its plant; and third, with many multinationals opting to standardize, it made business sense go with a supplier that can offer products, services, and support on a global scale.
“When global supply chain issues looked like they might upset the timescales, the end-user was open to change the platform, if needed,” Bergerhof explains, “but we found a remedy that saw parts being pre-ordered and stocked at S&D Service und Distribution GmbH, a Rockwell Automation channel partner company, which would help ensure availability when we needed it. Rockwell was able to allay any fears we had and, as a result, we are currently installing the first production machines, which will be used for test runs and pre-production measurements. Eventually all the machines at the customer’s facilities will be replaced, with the company keen to have fewer strategic suppliers based on trusted collaborations.
“This type of packaging is ideal for any market that needs to package products that do not require barrier protection,” Bergerhof concludes, “as full recyclability is an incredibly attractive proposition for any companies that are being subjected to ever-more stringent local and international sustainability legislation.”
To learn more, watch our video interview with Marcus Behrens of HDG, where he tells us more about this exciting project.
Published March 8, 2024