Recommended For You
Thanks to the constant evolution of technology, resulting in open connectivity coupled to modern automation solutions, smart manufacturing has morphed from an abstract concept to a technological reality.
As consumer demands continue to change rapidly, smart manufacturing can help to address these evolving requirements by taking advantage of emerging technology opportunities.
Smart manufacturing delivers measurable results by improving safety, increasing quality and optimizing plant performance. There are various elements of smart manufacturing including people, process and technology and most importantly how they all combine to underpin a holistic approach to smart solutions.
The true value of data
Real time data taken directly from a machine or operation is a primary benefit of smart manufacturing. However, if that data is not applied properly, or if no action follows, there is no benefit.
How many times have you walked into your manufacturing area to find operators guessing about an issue? To give your people the actionable information they need, your machines must provide contextual actionable insights that improve decision-making. This starts with your business model, understanding the challenges that impact Overall Equipment Effectiveness (OEE), and how decisions can be driven to the appropriate level to improve productivity, quality, safety and sustainability.
It is important to acknowledge that smart manufacturing is a process, not a project. Start with one machine, one cell, one line and review that data you can collect, analyze and present. Being intentional about your data strategy – when you need real time data, how you will collect it and how you will use it – provides you a metric for action and a way to gain value from the insights.
Smart manufacturing is a journey, not a destination. As technology evolves, so do the opportunities.
Being smart means leveraging historic and real time operational data in an efficient way to optimize your OEE by deploying smart technologies. Chances are you already have devices in your plant that can generate and deliver their own part of this vital operational data mix. However, it is important to note that simply tapping into these devices will give you data but not information. Smart devices do not make manufacturing smart on their own; they work with users of the information to make it smart.
With smart systems, from component to PLC, coupled to information gateway solutions designed specifically to work between OT and IT systems, the data you collect can be shared throughout your enterprise. Analytics provides the capabilities for you to monitor trends, spot weaknesses, highlight training gaps and predict downtime before they negatively affect your operations.
Smart software
Smart manufacturing can be defined as a system of connected devices that produce contextual information, allowing people to make the right decisions to drive the desired manufacturing outcomes and reach targeted improvements.
Any smart manufacturing system must include software systems that support:
Visualization: This includes MES layer integration, machine data visualization, and business unit alignment.
Optimization: Focuses on operational efficiency and productivity, application of analytics, and risk management.
User experience: Considers the abilities of any user, scalability from plant manager through to operator, and operational intelligence.
Smart manufacturing is your gateway to digital transformation. Use your connected smart devices to open new windows of visibility into processes. Leverage data and analytics to enable better and faster decision making.
Embrace digital
Digital technologies have revolutionized the way we live, work and play. As technologies continue to advance, we continue to become more reliant on the benefits they provide. This is particularly relevant to manufacturing.
The pressure is on to reduce costs, improve customer experience and increase profitability. Organizations that are embracing digital are disrupting business models with new value propositions.
Digital engineering is not an all or nothing strategy. There is no need to replace the tools that your workers know and like today. Instead, you can extend those tools digitally to improve how designers, production managers, technicians and others work. Start by reviewing your business and determine where you can do things smarter, faster or better using a digital approach.
There are five key areas where digital engineering can help to improve your business:
1. Design and prototyping
Virtual design and prototyping can help you build, test and evaluate machine designs digitally. This provides the capability for you to change what is possible in your business. This allows you to get machines to market faster; reduce risk in your designs; and, create higher-caliber, more customised machines.
With simulation software, you can apply physics to your 3D CAD model to bring it to life. This allows you to watch it run and see how it interacts with people or with other machines. It is even possible to bring the model into a VR environment to watch it perform in front of you as if you were on the plant floor.
If changes need to be made, these can be actioned in your digital twin design with just a few clicks rather than buying parts and spending days of labor to build a new prototype. It is not just digital twins that can help you get machines to market faster.
Design software that uses an open data exchange, for example, allows engineers to design a machine once and then import that design data in tools. This can help save hours of rewriting and remapping work on projects. The reusable code allows you to build on the success of existing machines, without redesigning from scratch.
2. Commissioning
Waiting until you bring a machine onsite to perform controls testing is a recipe for disaster. You would not know if your machine and its control system are aligned until you are standing next to your customer, with their start-up date approaching. You may discover that your machines operate below expectations or falls short of the specification. Fixing these issues at the last minute can be expensive and lead to missed deadlines.
Virtual commissioning can help you put an end to these problems. By creating a dynamic digital twin of both your machine design and the real operational logic of the control system, you can uncover issues earlier in the design phase, long before you bolt your machine into the floor of a customer’s plant. With virtual commissioning, you can exhaustively verify and demonstrate the operation of your machine and the controller, before any resources are committed to them.
Daifuku Webb uses simulation software to test the PLC code for its material handling system in-house, before they go to the field. In one airport project, this led to significant cost savings. “Ordinarily, our people spend many months in the field,” said Greg Swisher, senior controls engineer, Daifuku Webb. “And we were able to condense that time down to about a three-week period from the time our engineers hit the field to the time the customer took acceptance.”
“Ordinarily, our people spend many months in the field, and we were able to condense that time down to about a three-week period from the time our engineers hit the field to the time the customer took acceptance.” – Greg Swisher, senior controls engineer, Daifuku Webb.
3. Training
Virtual training eliminates the requirement to for both machines and operators to be onsite together. A digital twin allows you to train workers before a machine arrives. By either wearing a VR headset or working from a screen, workers can build skills and competency in a safe and immersive virtual environment. One of the greatest benefits of virtual training is the freedom it gives you.
It allows you to conduct training at anytime and from anywhere by delivering the flexibility to provide training to whoever needs it, whenever they need it and wherever they need it. Furthermore, virtual training does not have the same restrictions as real-world training. Workers can learn how to keep production running in ideal operations and they can be put to the test with simulated faults and extreme conditions that may not be possible to physically replicate. This can better prepare them for responding to similar incidents in production and ultimately reduce downtime.
Workers can be free to make mistakes in virtual training without worrying about disrupting production. If an operator does something wrong, that action can be recorded for remediation purposes. In addition, they can be required to prove their competency in training before they experience live production.
As seasoned workers retire and a new generation takes their place, virtual training can help workers learn their jobs in a more familiar way. They can use devices like tablets and VR headsets that they have at home and training can be enhanced in a virtual environment to gamify learning.
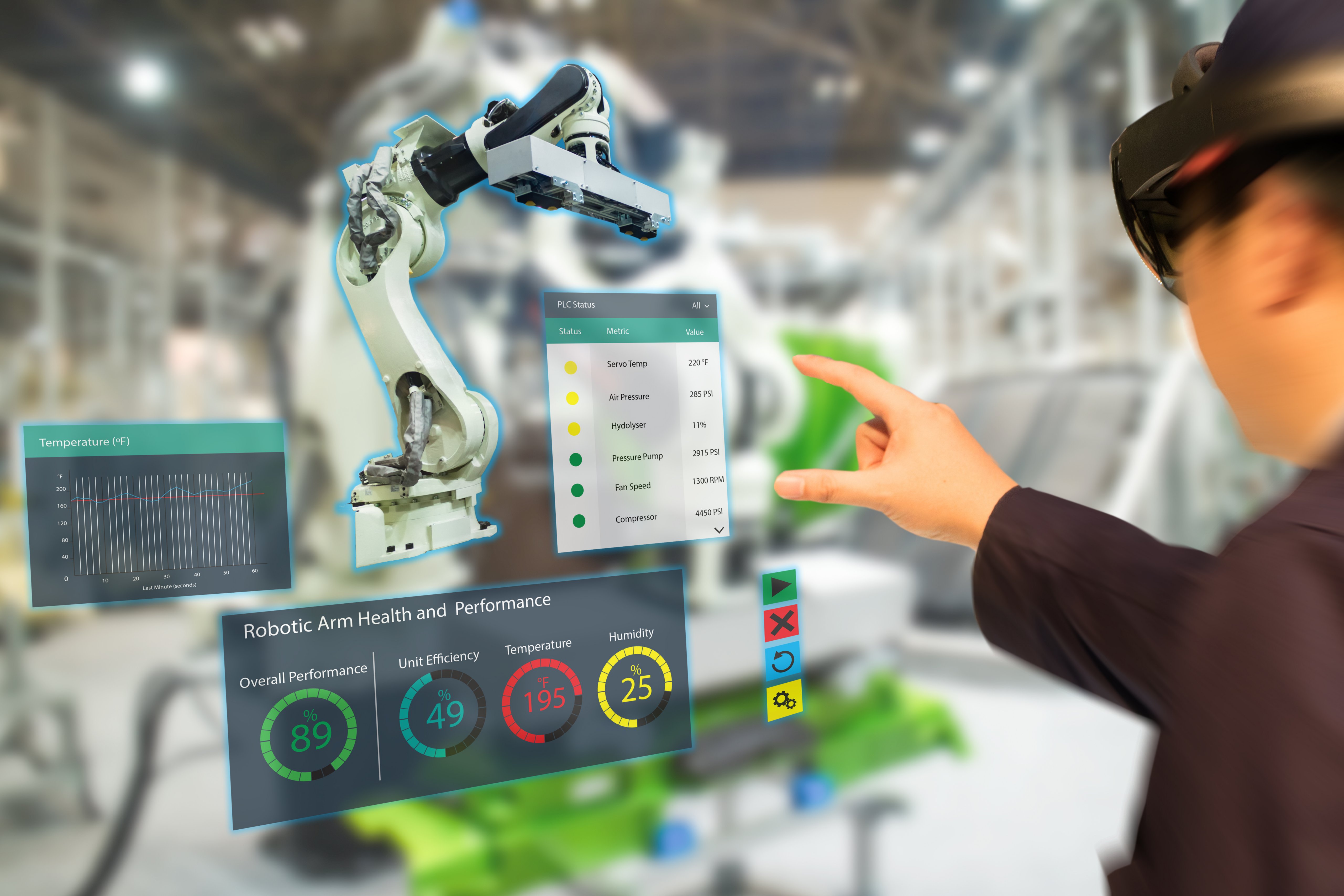
4. Operations
The value of digital engineering does not stop after machines are commissioned and operators are trained. Once production starts, digital twins can mimic processes, machines and controls to help plant personnel learn about operations and experiment with changes. An ever-growing digital thread of information can reveal insights into how production can be improved.
Operations of all types can reach new heights when they can continuously drive improvements in production and adjust on the fly using insights from your digital thread. Use trial line startups and production scheduling and sequencing to optimize product mixes and volumes. Experiment with machine configurations to improve quality, reliability and throughput.
In addition, you can use your digital thread to detect anomalies in processes to uncover operational issues before they impact quality and cause scrap downtime. You can test run new products or machines to optimize throughput and avoid problems like downstream bottlenecks – saving precious production time.
A global manufacturer implemented a digital thread alongside its MES and saw a 50% lead time reduction to customers, a 50% reduction in defective parts and a 4% improvement in productivity.
5. Maintenance
Maintenance teams can fight downtime like never before using digital simulations and real time or even predictive insights. Data flowing through a digital thread can help technicians detect problems as they happen, to prevent or minimize downtime. This includes health and diagnostic data from control system devices that can notify technicians when maintenance is needed. It also includes network data, for example, from switch level alarms, which today is just as critical to uptime.
In an ideal world, maintenance teams would never need to respond to downtime events because they could predict them. This is increasingly possible thanks to the use of predictive analytics. These analytics use machine learning and artificial intelligence to learn your operations, identify machine issues early and alert technicians of those issues. Technicians can then schedule maintenance during a planned downtime.
Digital twins can help you improve MTTR in a number of ways. First, virtual training allows technicians to prepare for downtime problems in advance rather than troubleshooting them the first time they happen. When problems do happen, technicians can use AR technology to overlay diagnostics or work instructions on a physical machine to diagnose and fix problems faster.
“As industrial organizations manage transitioning workforces, predictive analytics solutions can help ensure maintenance decisions and processes are captured and repeatable by incoming personnel.” – ARC Advisory Group, Digital Twins Roadmap: From Reactive to Prescriptive Maintenance.
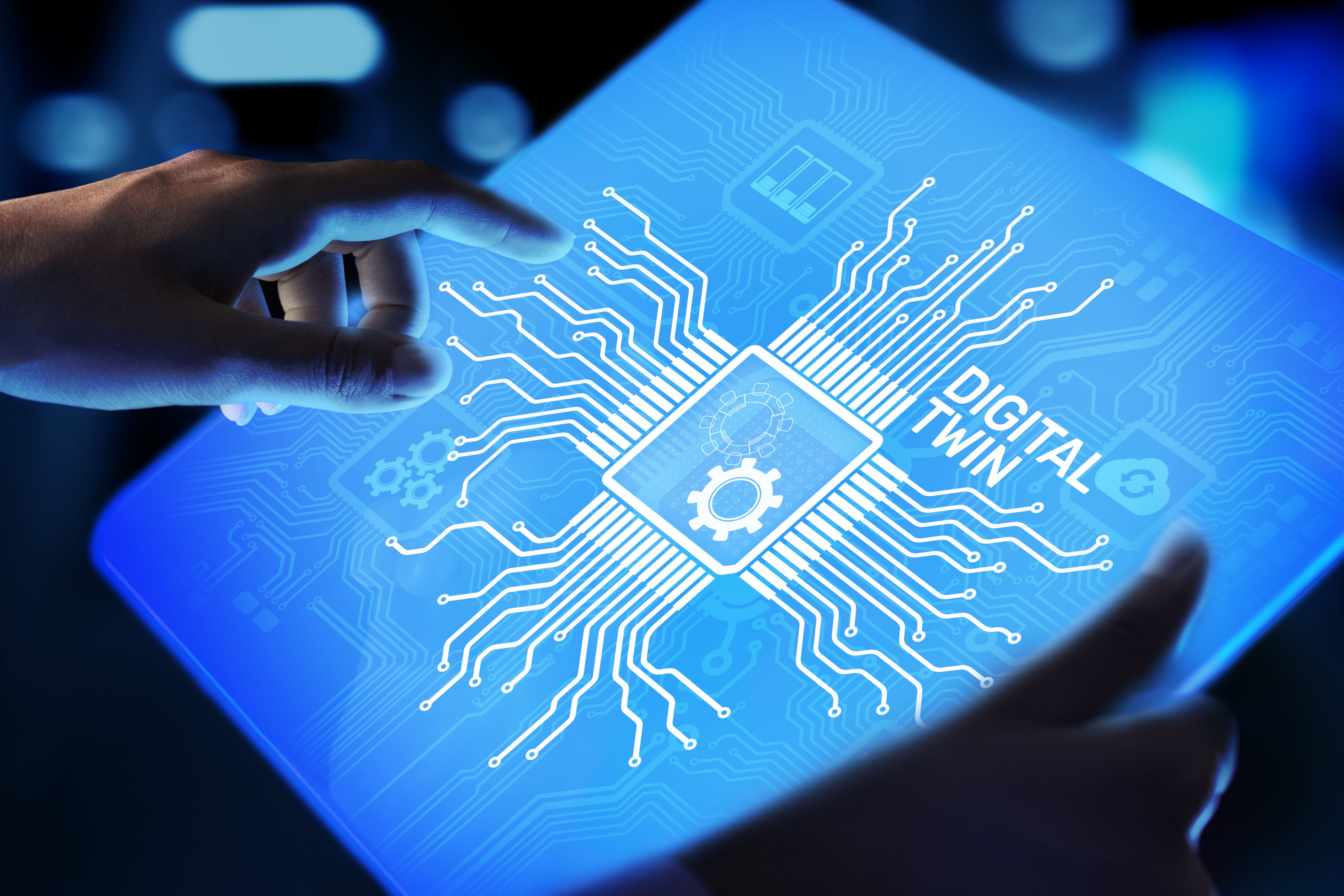
Smarter supplier solutions
No matter where you are on your digital journey it is worthwhile asking your suppliers for smarter, safer, more connected and secure machines, equipped with smart components and smart objects at the controller level. This means that when connected, all the data is there, organized and instantly usable – allowing you to get value the moment you connect.
As an end user, you must engage, specify and question OEMs. Ask yourself, “What additional value would I get if this machine deployed smart technology?” Then ask your OEM exactly the same question.
Price should not be the primary metric upon which you base your purchasing decisions. It is important to consider the whole life cost of the asset, including its operation and consumption, and the extra value that the data it generates can deliver. Work closely with your suppliers, explaining your smart aspirations and then challenge them to exploit technology that helps you reach your smart manufacturing goals.
Imagine if your operations could benefit from:
- Operational data that allows users to be more proactive and gain insights into their operations
- Faster return on investment and greater uptime
- A framework of design and operation tools that will simplify system integration, operation and maintenance
- Integration on a common platform
- Safety features that enhance both safety and productivity by improving machine access, reducing downtime and reducing restart time
- Secure remote access to speed diagnostics and troubleshooting while minimizing worker exposure to hazards
With smart manufacturing, this could now be your reality. By converging plant level and enterprise networks and securely connecting people, processes and technologies – you can redefine what is possible.
Redefine the possibilities
Now more than ever, businesses are stretched to do more with less. Adding to this, changing demographics are creating workforce challenges for manufacturers and industrial operators with retirement, economic expansion and technology evolution overwhelming companies’ abilities to staff operations.
Many contemporary business outcomes are based around knowledge-driven operations and smart, flexible manufacturing. Providing your operators, maintenance technicians, engineers, managers, and executives with actionable insights that optimize your workforce’s strengths and capabilities is a key element of smart manufacturing.
New insights that are revealed through better data access can help you reduce bottlenecks, implement demand-based decisions, and improve maintenance. Greater digitization can help you reduce downtime and improve profitability.
Benefit from collaborating in real time across the value chain, validating new lines and processes virtually, simplifying data science and increasing your manufacturing flexibility.
Digitally transform your operations to unlock the possibilities and improve almost any aspect of your enterprise performance.
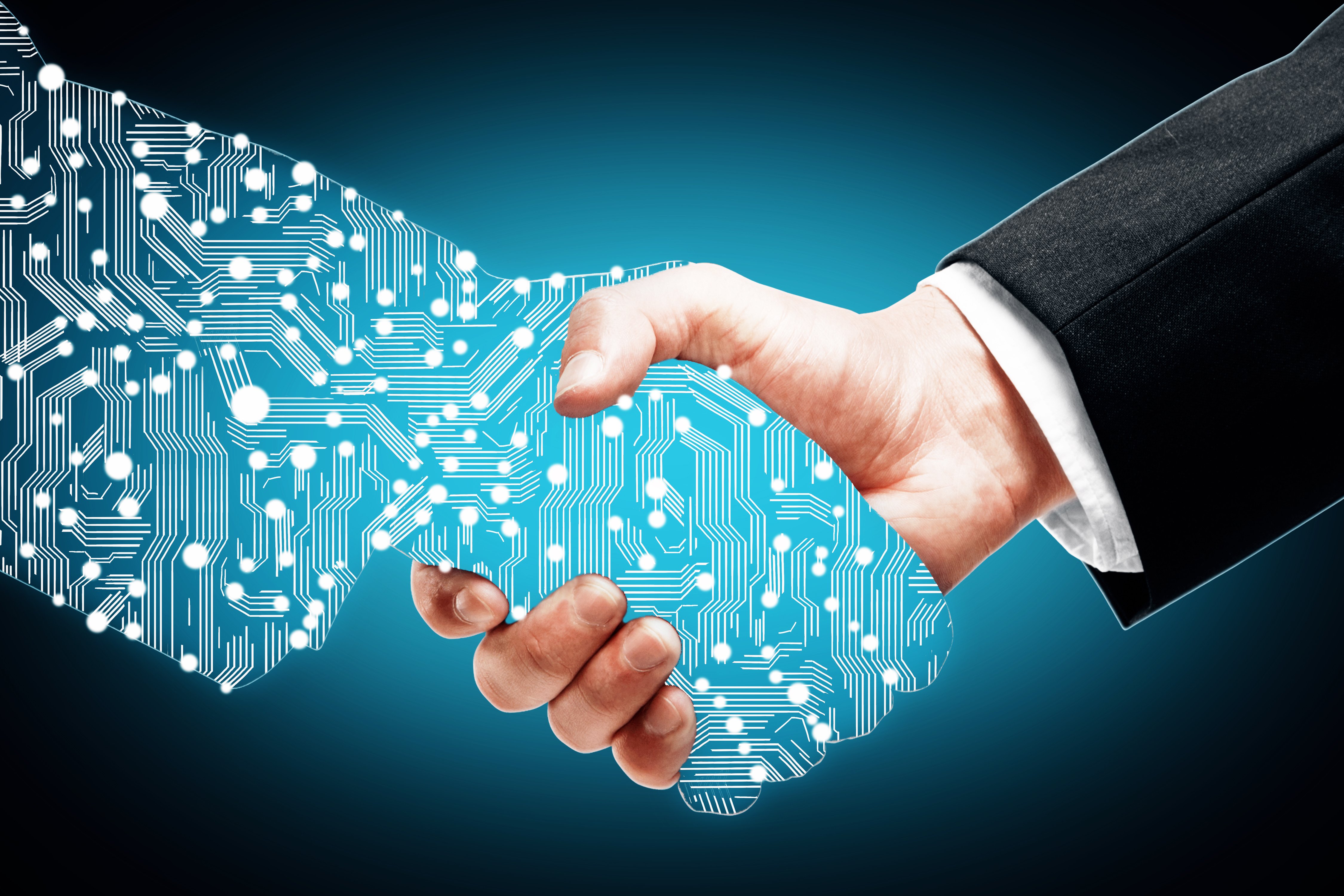