Recommended For You
Industry as we know it is changing rapidly – from a shortage of skilled workers and high turnover to advancements in connectivity and IoT. Innovation is driving us to augment in-house experience and institutional knowledge with intuitive technology and partner support.
To remain competitive, many companies are challenged to work faster, smarter and with greater agility at all phases of their enterprise lifecycle. The key goal is to optimize the investments you make in your machines, equipment and technology. However, this can be easier said than done.
How can you make the most out of your production assets, systems, plants and processes? LifecycleIQ Services from Rockwell Automation can help you to expand what is possible through active collaboration and support. Whether you are designing, operating, maintaining or innovating, our support can help you navigate the complexities and find success.
Defining the roadmap
The first step is to define the roadmap to meet your business outcomes. This involves generating a long-term plan based on innovative concepts and analytics that align with the business strategy. Lifecycle services can deliver proven outcomes to help you address aging infrastructure, reduce the workforce skills gap or achieve sustainable growth. These smart, connected services bring together industry, technology, operational and application expertise to enable safe, secure and reliable manufacturing.
We can partner with you using our digital technologies and expansive domain knowledge to enable you to be more productive every stage of the lifecycle. The roadmap to success can be defined in four key stages:
Innovate: Leverage our industry expertise to identify new opportunities to improve. Identify how to turn process and machine data into meaningful information for data-drive decision making. Use predictive analysis to reduce downtime. Accelerate the speed of innovation through knowledge, reuse, speed of change and access to information.
Whether it is a feasibility study, digital transformation initiative or modernization strategy – innovative technologies, services and solutions can help.
Design: Use intelligent insights to build a flexible design with system readiness and agility for future innovation and change. Leverage our domain expertise in system design and simulation, network design or as your main automation contractor to enable smart manufacturing.
By designing your networks, systems, and applications to be integrated and intelligent you can increase speed to market with early access to information. This also helps to reduce risk in your operation, with a digital backbone and enhanced cybersecurity.
Operate: Use application and technical expertise combined with scalable project delivery to improve your operations. Leverage our proven expertise for a better user experience. From installation and commissioning to project management and operational technology infrastructure as a service – we can help you achieve facility and process operational requirements.
Benefit from faster commissioning for faster time to value and improve operator performance and reduce training time with augmented and virtual reality tools.
Maintain: Our lifecycle services allow you benefit from one point of access to highly trained engineers. Connect your data, systems and processes to leverage information that helps you predict what is ahead. Reduce Mean Time to Repair (MTTR) through remote assistance.
Empower your operations to make better, faster decisions and improve operational excellence for ongoing production – discover new possibilities and transform them to reality.
Minimize risk to maximize productivity
If your equipment goes down, how prepared are you to recover quickly? Most companies require some level of outside support, especially as they contend with skills shortages, obsolescence risks and increasing operational complexity. Adding to this, is the growing pressure to maximize productivity and minimize operational risk. As a result, your ability to support, maintain and keep your current systems running optimally is critical.
LifecycleIQ services from Rockwell Automation combine digital technologies with our expansive domain knowledge to help your company address its greatest challenges at all phases of your enterprise lifecycle. The lifecycle services that we offer provide the long-term partnership you need and expect at all stages of your journey to enable safe, secure and flexible manufacturing.
Leverage digital insights to maintain optimal operations. Connect all of your data, systems and processes to provide you with the right information at the right time - information that can help you predict what’s coming, anticipate an issue before it happens, and make your business more connected, productive and intelligent.
LifecycleIQ Solutions in Action
LifecycleIQ services help enable you to expand what is possible through active collaboration and support. The use cases below detail how lifecycle services add value to a variety of applications including data center management, application support management and network management.
Data Center Management
A food company needed to improve server reliability to reduce the number of server issues it was experiencing. The Operational Technology Infrastructure services solution involved:
- Management of virtual environments and Industrial Data Centers
- Secure environment with managed deployments (patches, antivirus and firmware)
- Single point of contact for support
- Reduced time to implement by providing the design and implementation of the architecture
The result: A 90% reduction in troubleshooting time
Application Support Management
A global mining company needed to support their sites with proper personnel but was facing a skills gap. This made it difficult to manage the risk associated with supporting their global sites. The Application Support Management agreement provided:
- Consistent technical expertise to fill the skills gap and improve processes
- 50 hours per year of reduced downtime
- Global disaster recover solution to help mitigate safety risk
The result: $1.1 million saved annually
Network Management
A leading beverage company could see the potential value of enabling information convergence but was challenged with aging infrastructure, cyber hygiene risks and a legacy install base. Modernization was required to improve productivity, so they called on Rockwell Automation to provide LifecycleIQ services. The Managed Support solution delivered:
- A modernized network infrastructure
- Management of operational technology network assets
- Managed services to mitigate cyber risks
- Application support to reduce the cost of operations
- Design and implementation of the architecture deployed.
The result: The solution enabled a response time of only 10 minutes or less
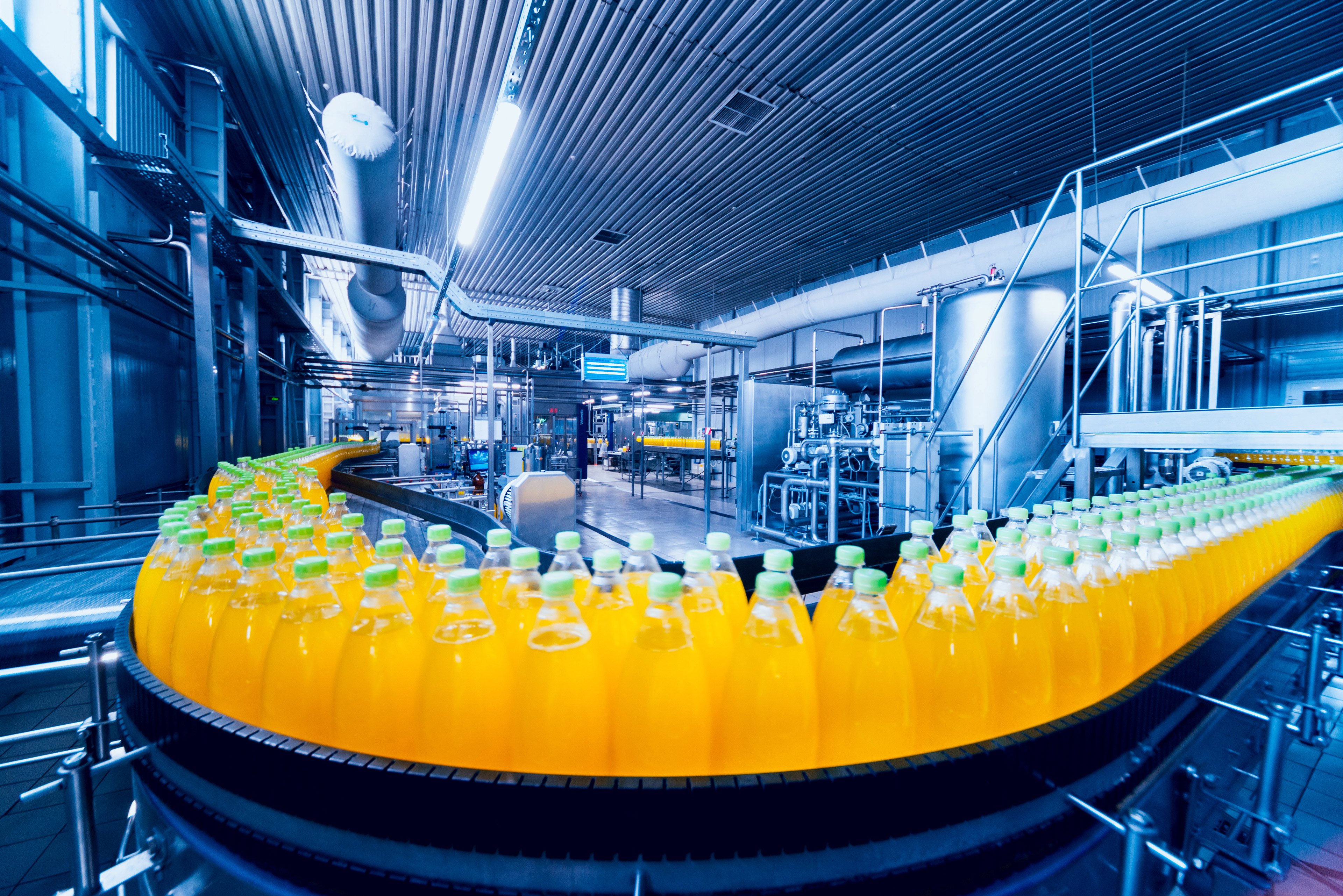