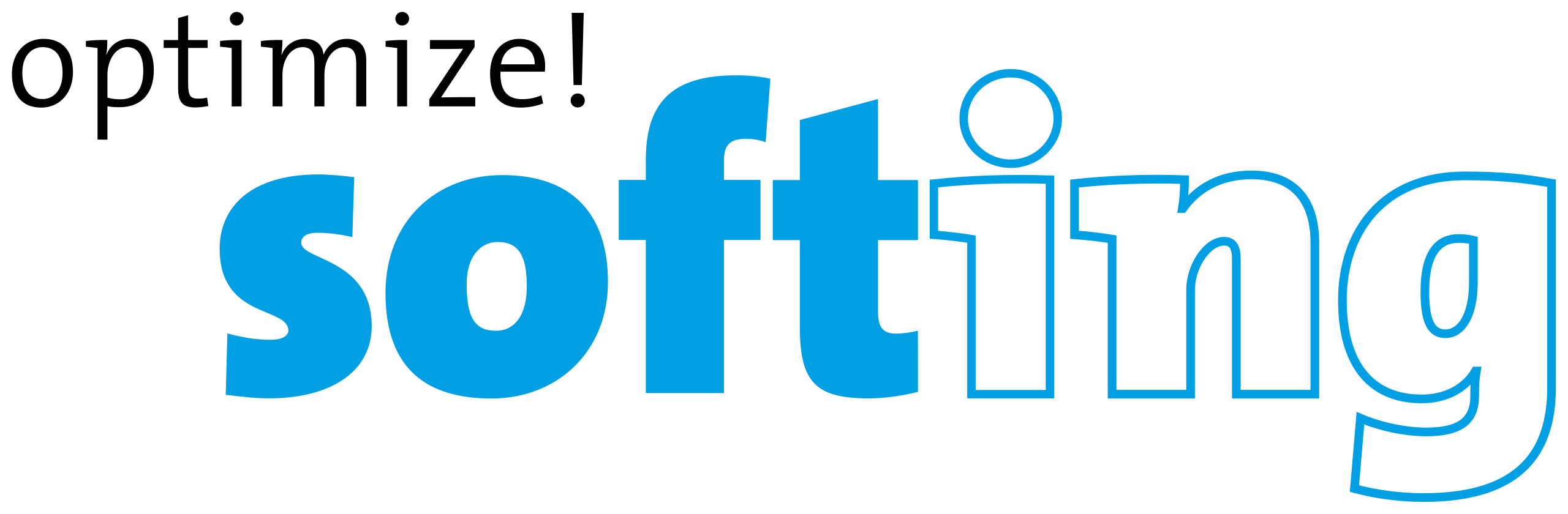
Softing Industrial Automation is a world leading provider of industrial communication products and technologies for manufacturing and process automation.
- Product formulation requires running multiple test batches to optimize results, then repeating the most successful test run as the final production run
- Needed to bring product to market quickly
- ControlLogix® PLC from Rockwell Automation
- tManager® Enterprise Application Transaction Module from Softing
- Quick development of a new packing peanut material formulation and scaled production across four plants
Challenge
Developing a Sustainable Packing Peanut
Recently, a North American manufacturer was approached with a challenge: develop a packing peanut that will have less impact on the environment. The new packing peanut should use the same manufacturing processes and be produced on the same extrusion equipment. It should also meet the same quality standards as standard packing peanuts.
The manufacturer knew they would need to conduct hundreds of production runs as they innovated and tested various ideas. For each ‘run,’ it would be critical to capture detailed information that showed how each iteration performed. Parameters like barrel temperature, screw speed, and feed moisture content can change the test output’s bulk density, hardness, and water absorption index. All of these would affect how the final packing peanut would perform in real-life conditions and would need to be tracked.
To accelerate product development and better capture on-demand production data from each test run, the manufacturer approached Softing Industrial Automation, a member of the Rockwell Automation PartnerNetwork. Together, they decided to use the tManager Enterprise Application Transaction Module (eATM) to speed time to market.
Solution
tManager Improves Data Collection and Analysis
The tManager eATM is an in-chassis module that enables bi-directional data exchange between SQL databases and Rockwell Automation ControlLogix® PLCs. The module makes it easy to pull data out of the PLC and place it into an SQL database. Once the data is there, it can be used for anything from reporting and analytics to feeding order processing systems.
“The purpose of the tManager eATM is to digitally transform a PLC,” says Deane Horn, Softing’s Director of Marketing. “It evolves from just controlling the process to becoming more self-aware and having context for business decisions. Quality monitoring, track-and-trace, performance monitoring, tracking your KPIs, and downloading recipes are just a few of the applications that the tManager eATM enables by connecting PLC’s to business systems. The module enables this without writing code, adding a PC, or needing any OPC protocol translation.”
And that’s not all, according to Deane. “The tManager eATM is bi-directional, which means that it can either read data from SQL and write it to tags in the ControlLogix PLC, or it can read tags from the PLC and write them to the SQL database. The module does this with no impact to PLC performance.”
For this project, the manufacturer installed the tManager eATM on the extrusion machine that they would be using to produce the new packing peanuts. Their hope was to capture data from test runs, catalog it, and learn quickly which parameters were successful. This intelligence would enable faster time to market.
The tManager eATM captured around 90 data points during production runs, including flow rates, temperature zones, and pressures. Upon capturing this data, the module tied the process parameters used during that run to the specific samples. The process data was time-stamped important for auditing the individual factors contributing to the results of a particular test run, and for accurately replicating results in future runs.
Data capture rate was also an important consideration. If the data capture rate was too low, then the manufacturer might not be able to collect enough useful data. If it was too high, they could find themselves wasting time weeding through unnecessary levels of data. The manufacturer was able to adjust the data capture rate on the tManager eATM so they could zero in on the data that mattered the most.
Result
Speed to Market
Thanks to a combination of the manufacturer’s unique approach to product development and data capturing and time stamping capabilities from the tManager eATM, the manufacturer was able to successfully identify an optimized material formulation for sustainable packing peanuts. They have since scaled up production of the new packing peanut across four manufacturing plants.
The manufacturer was so happy with the use of the tManager eATM on this project that they have begun using it to support development work on other projects – testing ideas and production techniques for products like pet food, aquatic feed, and alternative proteins.
Published December 11, 2023