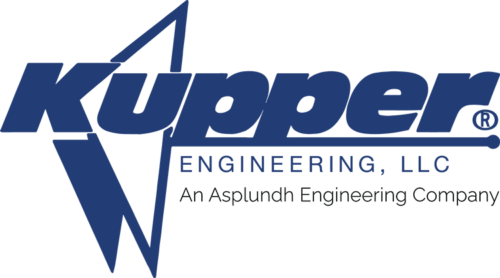
Kupper Engineering is a member of the Asplundh Infrastructure Group, a leading national alliance of infrastructure services and solutions for utilities, power producers, and energy-intensive customers. Kupper Engineering provides superior, full service professional engineering, engineering support, equipment procurement, and automation controls integration – from planning and design to implementation and commissioning.
- Design a system to convert landfill gas into renewable natural gas (RNG)
- Implement at 20 RNG plants between now and 2026
- System comprised of dozens of actuators, motors, valves, pumps and sensors – built on ControlLogix® and CompactLogix™ control systems, intelligent motor control centers, variable frequency drives and other components
- Ability to monitor and detect gas leaks, control ventilation, adjust fans, and shut systems down if needed
- At each of the 20 sites, converts between 3,000 and 8,000 standard cubic feet per minute of landfill gas into renewable natural gas
From food and dairy operations to landfills, Kupper Engineering is helping companies convert waste and related byproducts into renewable natural gas (RNG.) Made from biogas emitted from organic waste, RNG is processed to pipe-line quality standards and used as a substitute for fossil fuels.
Kupper, a provider of engineering, controls, and procurement services, was one of the first firms to provide electrical engineering services for RNG production facilities. They’ve supported about 30 RNG projects and have another 30 planned during the next three years. These include RNG sourced from landfill gas, and animal and food waste using anaerobic digester systems.
“Rather than digging natural gas out of the ground, which is ‘non-renewable,’ we’re taking a byproduct of human processes and turning it into a resource for people to use in their everyday lives,” said Jude Matteo, principal systems integrator, Kupper Engineering.
“What makes us unique is that as both an engineering and controls firm we understand how all the pieces fit together in these highly specialized projects,” added William Moss, a Kupper senior project manager. “We’re intimately involved from the initial design to implementation and support throughout the life of these sites.”
As part of its solutions portfolio, Kupper has relied on Rockwell Automation for more than a decade.
Challenge
Quality and Control are Paramount
Kupper is helping one of North America’s largest landfill operators aggressively expand its RNG infrastructure as part of its growth and sustainability strategies.
“Historically, as trash was buried in landfills it decomposed. This created off gases that smelled, could be extremely dangerous when accumulating, and negatively impacted the environment and ozone,” Matteo explained. “The original way operators dealt with that was to remove the landfill gas and flare it – just burn it off. Now through a series of processes, they can take that gas out of the landfill, clean it, and turn it into what is essentially natural gas.”
This operator plans to use the RNG generated to help fuel its transportation fleet and then return the remainder to the natural gas pipeline. Process control is paramount as stringent guidelines govern the process of converting landfill gas (LFG) to pipeline, quality gas.
“Landfill gas typically is 50% methane and then has a large amount of carbon dioxide (CO2) and a smaller amount of trace components. The CO2 and trace amounts need to be stripped away so the final product is 98% pure methane,” said Michael Markham, a Kupper senior project manager. “There are several processes to go through and each stage may require compression, cooling, heating and filtration.”
With dozens of actuators, motors, valves, pumps, and sensors, it’s a complex system to design, connect, and control. That’s why Kupper uses Rockwell Automation products, including ControlLogix® and CompactLogix™ control systems, intelligent motor control centers, variable frequency drives and other components in many of its LFG to RNG projects.
These technologies are also key to employee and system safety. They help facilities monitor and detect gas leaks, control ventilation, adjust fans, and shut systems down if needed.
Solution
Standardized Plant Design and Equipment
“We were asked to get involved with this client because they wanted to standardize plant design and equipment across various project sizes so they would be safe, reliable and consistent,” Markham explained.
Between now and 2026, the client plans to build 20 RNG plants in four sizes ranging from 16,000 to 30,000 square feet. These plants will have the capability to handle between 3,000 and 8,000 standard cubic feet per minute of LFG.
“These facilities will run fast acting, complex processes with hundreds of components that need to be installed, configured and integrated. When we use Rockwell Automation products, it’s by far the easiest and quickest way to do it,” Matteo said. “Since we know we’re going to build more of these plants, we try to template them. The ability to standardize and modularize programming has been straightforward, and we can count on the performance of Rockwell’s offerings.”
All of which is essential to maximizing production time.
“Whether it’s digester or a landfill, as in the case of this client, they're always making gas that has to be dealt with continuously. Any time a plant is not running, they have to do something with the gas and usually that means flaring it,” Matteo explained. “So, any increase in reliability is hugely beneficial.”
Result
Potential Economic and Environmental Benefits
Kupper’s first standardized LFG to RNG site for this client’s current portfolio went online in spring 2023 with about eight more expected in 2024 and the remainder in the years following.
An average site has the potential to recover and produce more than 780,000 MMBtu per year of RNG. MMBtu is the common metric used to measure heating content and fuel value. That amount equals serving more than 26,000 homes or 676 heavy-duty trucks annually and is the equivalent of more than 5.3 million gallons of diesel fuel. The use of RNG from this sized plant, instead of fossil fuels, has the potential to eliminate more than 50,000 tons per year of greenhouse gas emissions.
“We’re helping this client turn a nuisance gas byproduct into usable energy,” Markham said. “Instead of them having to spend capital and annual funds for disposal, they’ll produce a viable energy source that’s better for the environment and generates a profitable income.”
Visit our Renewable Energy Page to learn more about how we are helping companies accelerate the energy transition.
Published November 15, 2023